What Is Vision-Guided AGV? How Vision-Guided AGVs Are Used for Material Handling?
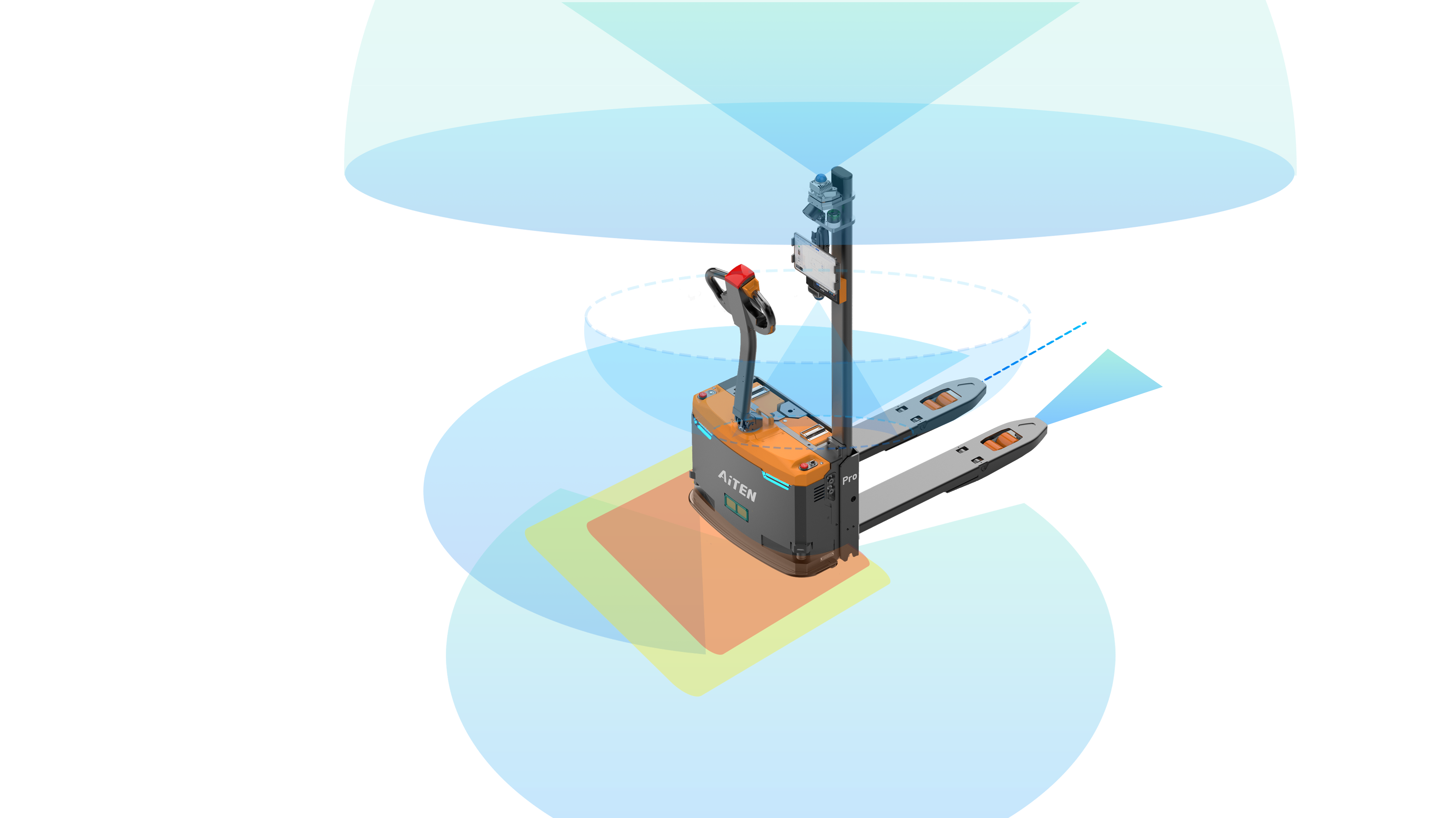
1. What is Vision-guided AGV?
Vision-guided AGV is a rapidly developing and mature AGV. This type of AGV is equipped with a CCD camera and sensors, and an on-board computer is provided with an image database of the surrounding environment of the AGV's intended driving route.
Vision-Guided AGVs can be installed with no modifications to the environment or infrastructure. They operate by using cameras to record features along the route, allowing the AGV to replay the route by using the recorded features to navigate.
Vision-Guided AGVs use Evidence Grid technology, an application of probabilistic volumetric sensing, and was invented and initially developed by Dr. Hans Moravec at Carnegie Mellon University. Evidence Grid technology uses probabilities of occupancy for each point in space to compensate for the uncertainty in the performance of sensors and in the environment. The primary navigation sensors are specially designed stereo cameras.
The vision-guided AGV uses 360-degree images to build a 3D map, which allows the vision-guided AGVs to follow a trained route without human assistance or the addition of special features, landmarks or positioning systems.
Vision-guided AGVs offer significant benefits in industries requiring dynamic and flexible logistics solutions, contributing to the growing trend toward smart factories and Industry 4.0.
2. How Vision-Guided AGVs Are Used for Material Handling?
AGV system is a robot fitted with one or more cameras used as sensors to provide a secondary feedback signal to the robot controller for a more accurate movement to a variable target position. The vision-guided AGV is rapidly transforming production processes by enabling robots to be highly adaptable and more easily implemented, while dramatically reducing the cost and complexity of fixed tooling previously associated with the design and set up of robotic cells, whether for material handling, automated assembly, agricultural applications, life sciences, and more. In one classic but rather dated example of vision-guided AGV used for material handling, the vision system (camera and software) determines the position of randomly fed products onto a recycling conveyor. The vision system provides the exact location coordinates of the components to the robot, which are spread out randomly beneath the camera's field of view, enabling the robot arm(s) to position the attached end effector (gripper) to the selected component and pick from the conveyor belt. The conveyor may stop under the camera to allow the position of the part to be determined, or if the cycle time is sufficient, it is possible to pick a component without stopping the conveyor using a control scheme that tracks the moving component through the vision software, typically by fitting an encoder to the conveyor, and using this feedback signal to update and synchronize the vision and motion control loops.Such functionality is now common in the field of vision-guided AGV. It is a rapidly evolving technology that is proving to be economically advantageous in material handling and skilled labor costs by reducing manual intervention, improving safety, increasing quality, and raising productivity rates, among other benefits.
Currently, AiTEN does not offer vision-guided AGVs. However, our products such as the APe15 and MP10s are already delivering outstanding performance across a wide range of industries, meeting diverse industrial automation needs.If you are looking to upgrade your operations with intelligent AGV solutions, contact AiTEN today. We offer free feasibility analyses tailored to your specific operational environment, helping you find the best-fit automation solution for your smart factory transformation.