Are Unmanned Forklifts and AGV Forklifts the Same? AGV Unmanned Forklift Working Principle Analysis
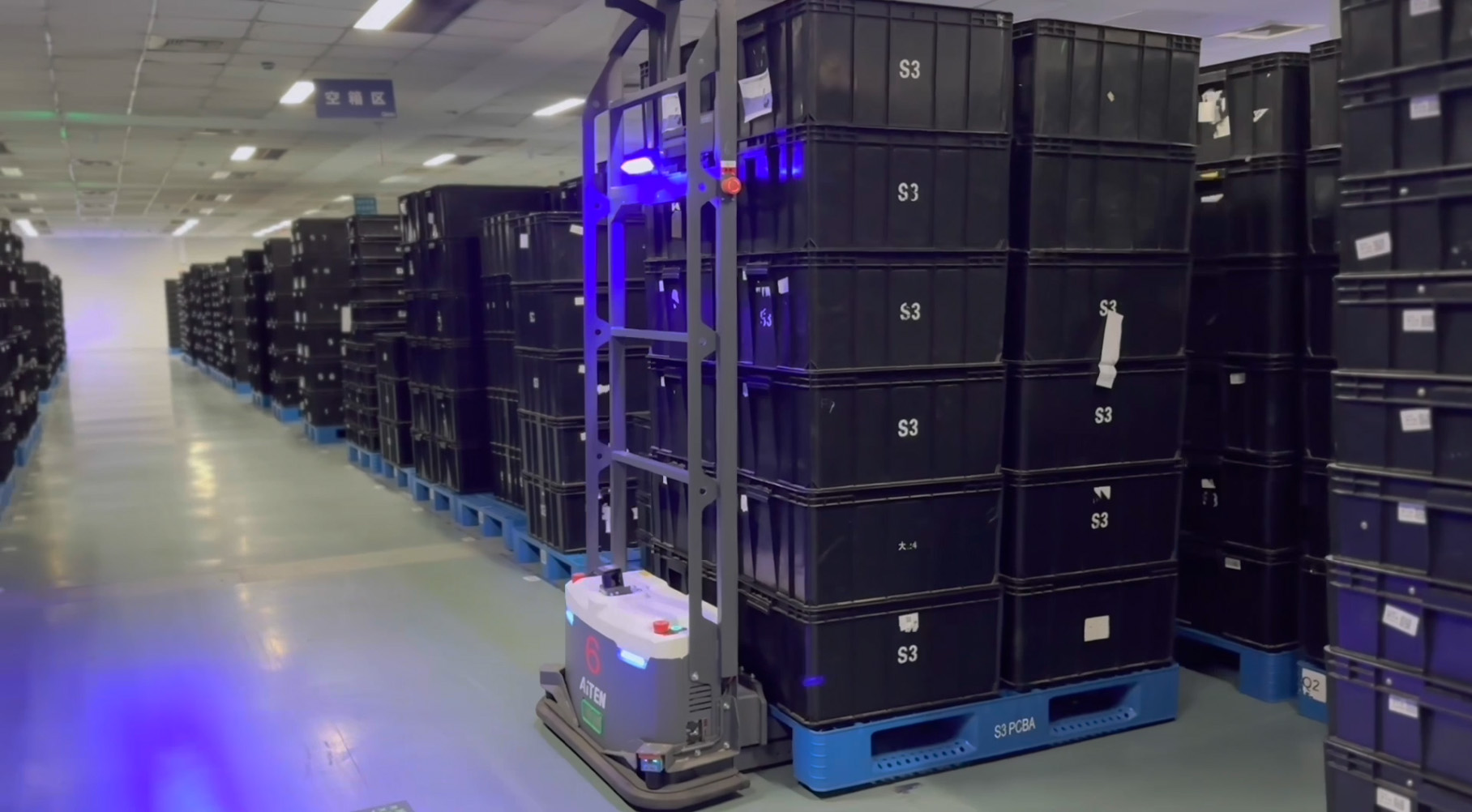
Are Unmanned Forklifts and AGV Forklifts the Same?
In the field of intelligent manufacturing and intelligent logistics, ‘unmanned forklift’ and ‘AGV forklift’ are often used interchangeably, but there are subtle differences in their technical definitions and application scenarios. Unmanned forklift is a broad concept that refers to all automated forklift equipment that does not require a human driver, including remotely operated, semi-automated and fully automated types, and whose core feature is to realise cargo handling using autonomous navigation technology.
AGV forklift (Automated Guided Vehicle Forklift) is a typical form of unmanned forklift, which refers to the intelligent handling equipment equipped with an automatic guidance system (such as LIDAR, magnetic navigation, etc.) with core functions such as autonomous navigation, path planning, obstacle avoidance and task scheduling.
From the technical dimension, AGV unmanned forklifts need to meet the following core characteristics:
1. Autonomous navigation capability: relies on laser, magnetic stripe or vision navigation technology, without relying on fixed tracks or manual intervention;
2. Intelligent control system: integrating task scheduling, obstacle avoidance algorithms and real-time data interaction functions;
3. System compatibility: can be seamlessly interfaced with WMS (warehouse management system), ERP (enterprise resource planning) and other platforms.
In contrast, non-AGV unmanned forklifts may only have basic remote control functions or limited automation capabilities, and are unable to realise dynamic decision-making in complex environments. For example, omnidirectional forklift AGVs, as the higher-order form of AGVs, support 360° movement and narrow-aisle operations, and their flexibility and efficiency far exceed that of traditional unmanned forklifts.
How AGV Unmanned Forklifts Work?
How Do Automated Forklifts Work? The Future of Material Handling
AiTEN Robotics In-Depth Analysis: The Road to Technology Breakthrough for Material Handling Robots
The efficient operation of AGV unmanned forklifts relies on the synergy of five core systems.
1. Navigation and Positioning System
AGV forklift trucks sense the environment through sensors such as LIDAR, vision cameras or inertial navigation (IMU), and combine them with SLAM algorithms to build real-time maps and achieve centimetre-level positioning accuracy. For example, AiTEN Robotics' mini-handling AGV forklift MP10S supports a variety of advanced technologies such as 2D and 3D laser SLAM navigation, and can still navigate accurately in dynamic environments.
2. Route Planning and Scheduling System
Based on the task instructions (e.g. ‘carry goods from point A to point B’), AGV forklift trucks calculate the optimal path through path planning algorithms (e.g. AI algorithm) and interact with the centralised scheduling system (e.g. WMS, MES) in real time to dynamically adjust the priority of the task and the route of the vehicle. For example, when multiple AGVs work together, the system will automatically assign tasks to avoid path conflicts.
3. Power and Drive System
Powered by lithium batteries or super capacitors, the drive motor is connected to the wheels through a gearbox to realise forward, backwards and steering movements. Some high-end AGV forklift trucks support automatic charging and can return to the charging post to replenish energy when the power is lower than the threshold.
4. Cargo Handling and Execution System
Gripping, lifting and placing of goods are done by robotic arms, forks or clamping devices. For example, the stacking AGV forklift can accurately stack the goods to the designated position on the shelf within ±10 mm.
5. Safety Protection and Communication System
Equipped with 360° LIDAR, ultrasonic sensors and anti-collision strips for obstacle detection and emergency braking. At the same time, it communicates with the host computer through 5G or Wi-Fi network, transmitting real-time status data and task instructions.
AiTEN Robotics Cases
Automatic Transfer of Materials by AGVs in Conjunction with Three-dimensional Warehouse Shuttles
Efficiency Increased by 50%: AiTEN’s Narrow Aisle Handling Solution for the Automotive Industry
Ready to explore adapted AGV unmanned forklifts for your business? Contact AiTEN Robotics for a free consultation on your needs.