What Is the Key Difference Between AMR and AGV?
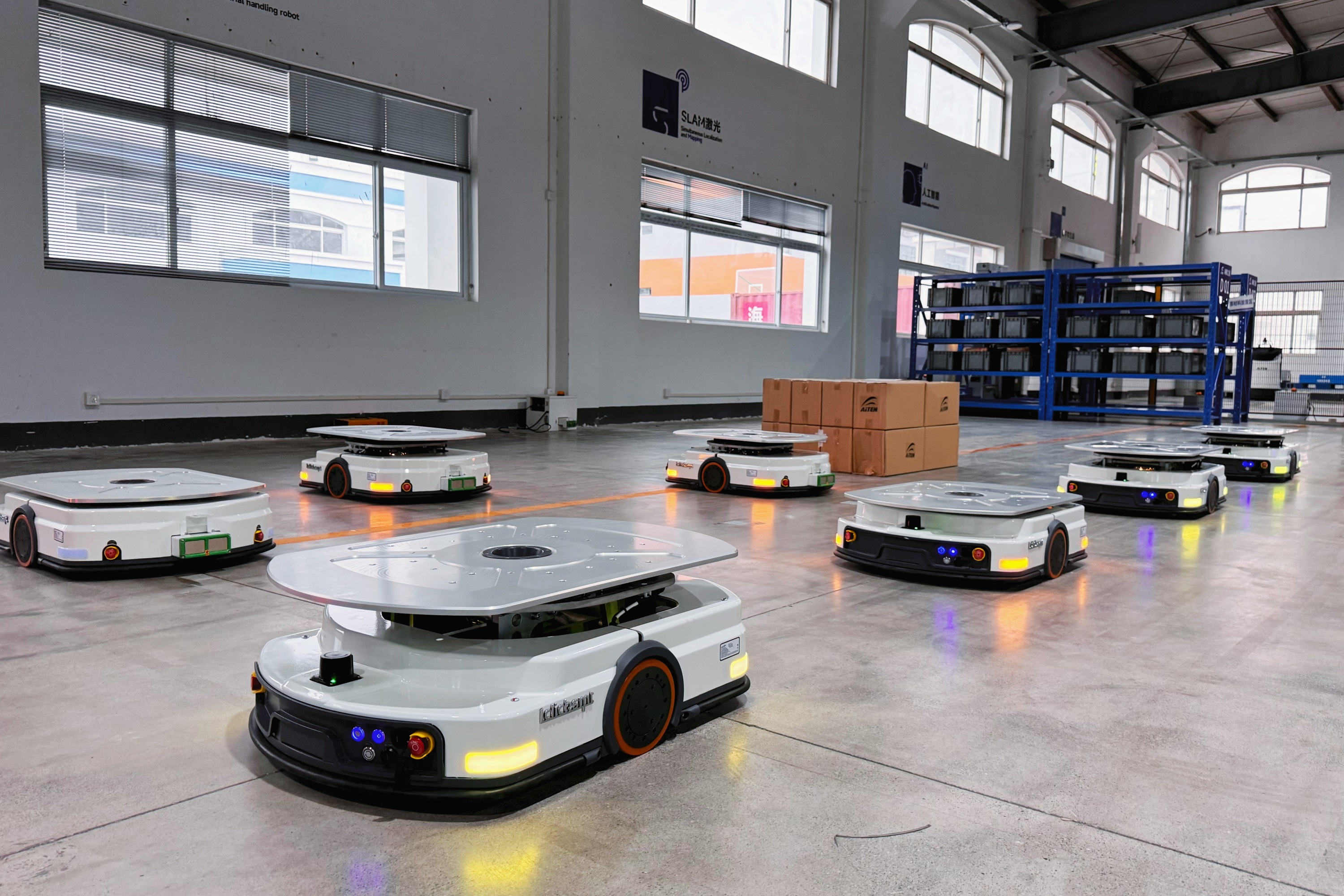
In the field of industrial logistics automation, although AMR (Autonomous Mobile Robot) and AGV (Automated Guided Vehicle) are both aimed at achieving the core objective of material handling, there are significant differences in their technical characteristics, application scenarios, and development trends, and at the same time, there is a certain trend of functional integration in the technology iteration.
1. Navigation and Path Planning
- AGV (Automated Guided Vehicle): relies on a pre-set path (e.g. magnetic stripe, guideway, QR code or laser reflector), travels on a fixed route, is unable to avoid obstacles dynamically, and is less flexible. If the path is blocked, it will stop running and require human intervention.
- AMR (Autonomous Mobile Robot): builds a map of the environment in real time by means of sensors (LIDAR, cameras, etc.) and SLAM (Simultaneous Localisation and Map Construction) technology, plans the path autonomously, avoids obstacles dynamically, and has high flexibility.
2. Deployment and Flexibility
- AGV: Traditional AGV mission process is solidified, need to lay physical guidance facilities (such as magnetic strips, guide rails), long deployment time, high transformation costs, but AiTEN AGV unmanned forklift trucks by upgrading the navigation system, higher flexibility, do not need to lay physical guidance facilities, and the fastest half an hour can be completed on-site deployment.
- AMR: No infrastructure is needed; it can work by setting up virtual maps through software, with fast deployment and flexible path adjustment, which is suitable for changing business needs.
3. Intelligent
- AGV: running based on programmed instructions, a lack of environmental awareness and autonomous decision-making ability, belongs to ‘automation’ equipment.
- AMR: equipped with an AI algorithm and edge computing capability, it can analyse the environment, optimise the path and adapt to dynamic scenes, and belongs to ‘autonomous’ robots. It supports multi-machine collaboration and IoT communication, and can be linked with a warehouse management system (WMS), lift, robotic arm, etc., to achieve complex task collaboration.
However, AiTEN's AGVs have been upgraded to achieve AMR autonomy.
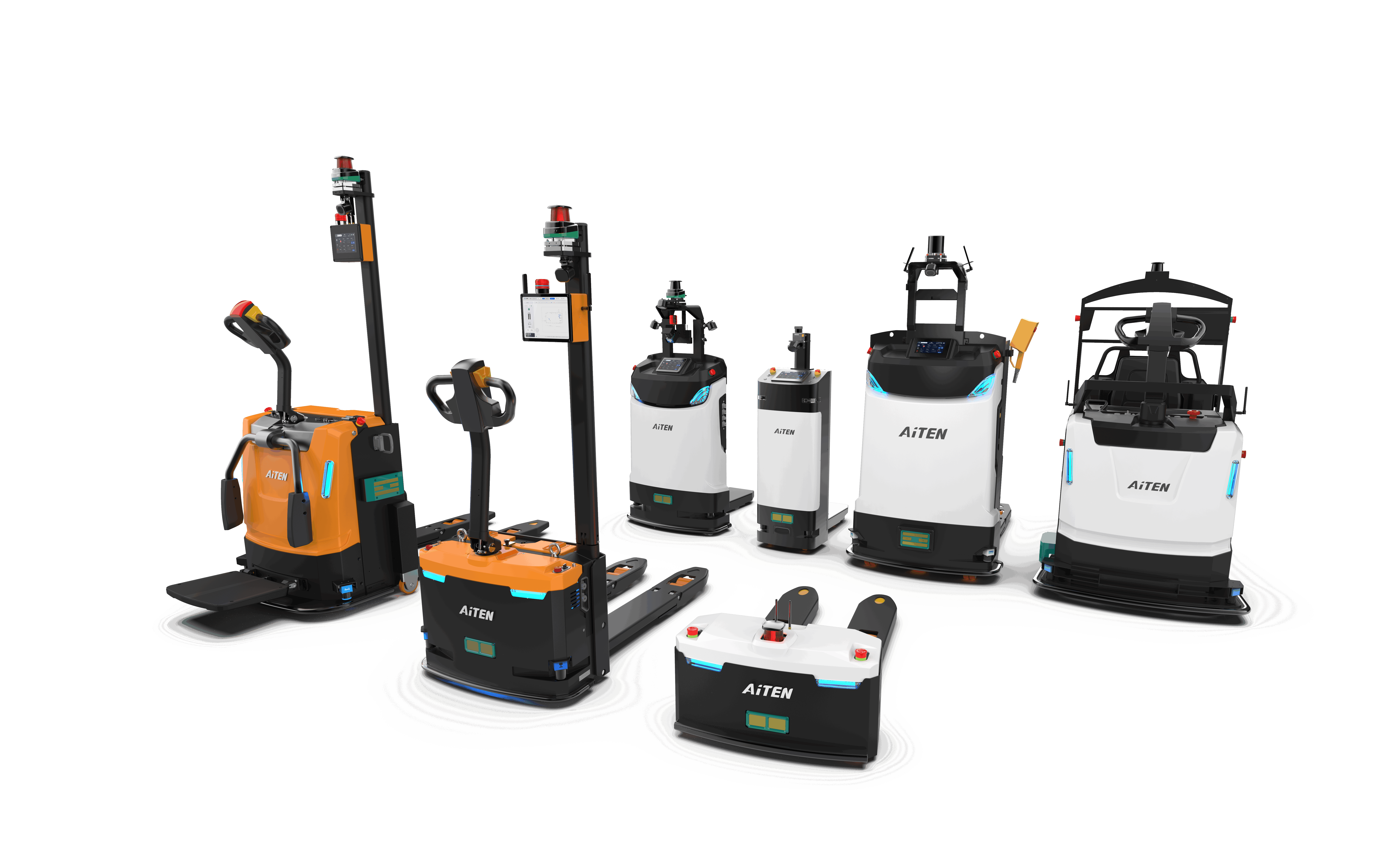
4. Application Scenarios
- AGV: Highly repetitive scenarios such as automotive manufacturing.
- AMR: E-Commerce warehousing and sorting, hospital material distribution, flexible manufacturing and other complex environments that require frequent layout adjustments.
Cases:
Efficiency Increased by 50%: AiTEN’s Narrow Aisle Handling Solution for the Automotive Industry
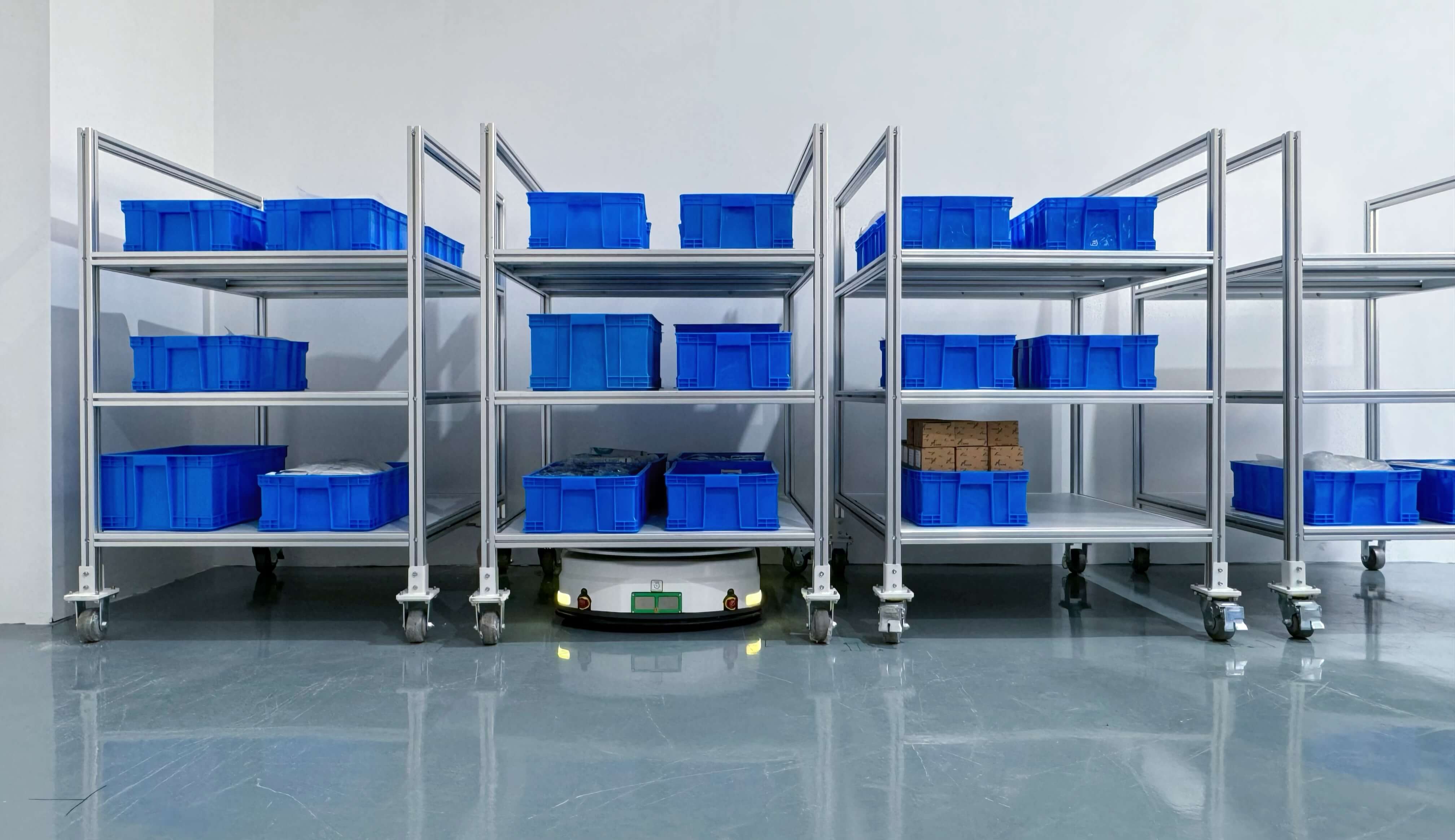
5. Technology Evolution Trend
- Intelligent upgrading of AGVs: Some AGVs have begun to integrate SLAM technology, such as AiTEN Robotics' “hybrid navigation” models, which are capable of completing handling tasks without the need to lay physical guidance facilities.
- Multi-machine cooperation and cloud platform: AiTEN's RDS scheduling system supports 100 AGVs to run in mixed operation, and solves traffic conflicts through virtual electronic fence and dynamic avoidance strategy, which improves efficiency by 50%.
Conclusion
The essence of the difference between AMR and AGV lies in the technical route of ‘automation’ and ‘autonomy’, but with the advancement of technology, the functional boundaries between the two are being broken. In the future, the synergy of the two types of equipment, cloud control or become the mainstream paradigm of industrial logistics.
As an enterprise in the field of intelligent logistics solutions, AiTEN Robotics always focuses on ‘smart factory’ scenarios, deeply integrates technological innovation and industry demand, and has provided comprehensive services for more than 200 manufacturing customers around the world: relying on the full series of AGV unmanned forklift product matrix to cover a variety of handling scenarios, and self-researching industry-level intelligent dispatching system to achieve efficient collaboration of multiple equipment. The self-developed industry-level intelligent scheduling system achieves efficient collaboration of multiple devices, and through the full life cycle service system covering pre-sales planning, deployment and implementation to operation and maintenance optimisation, it helps enterprises to achieve intelligent transformation of warehousing and logistics, and continues to empower the manufacturing industry with digital upgrading and high-quality development.
If you want to explore solutions for your smart factory, please contact us, and we will provide you with free feasibility analysis based on your operational situation.