Analysis of the Core Differences and Advantages Between Unmanned Forklift Trucks and Traditional Forklift Trucks
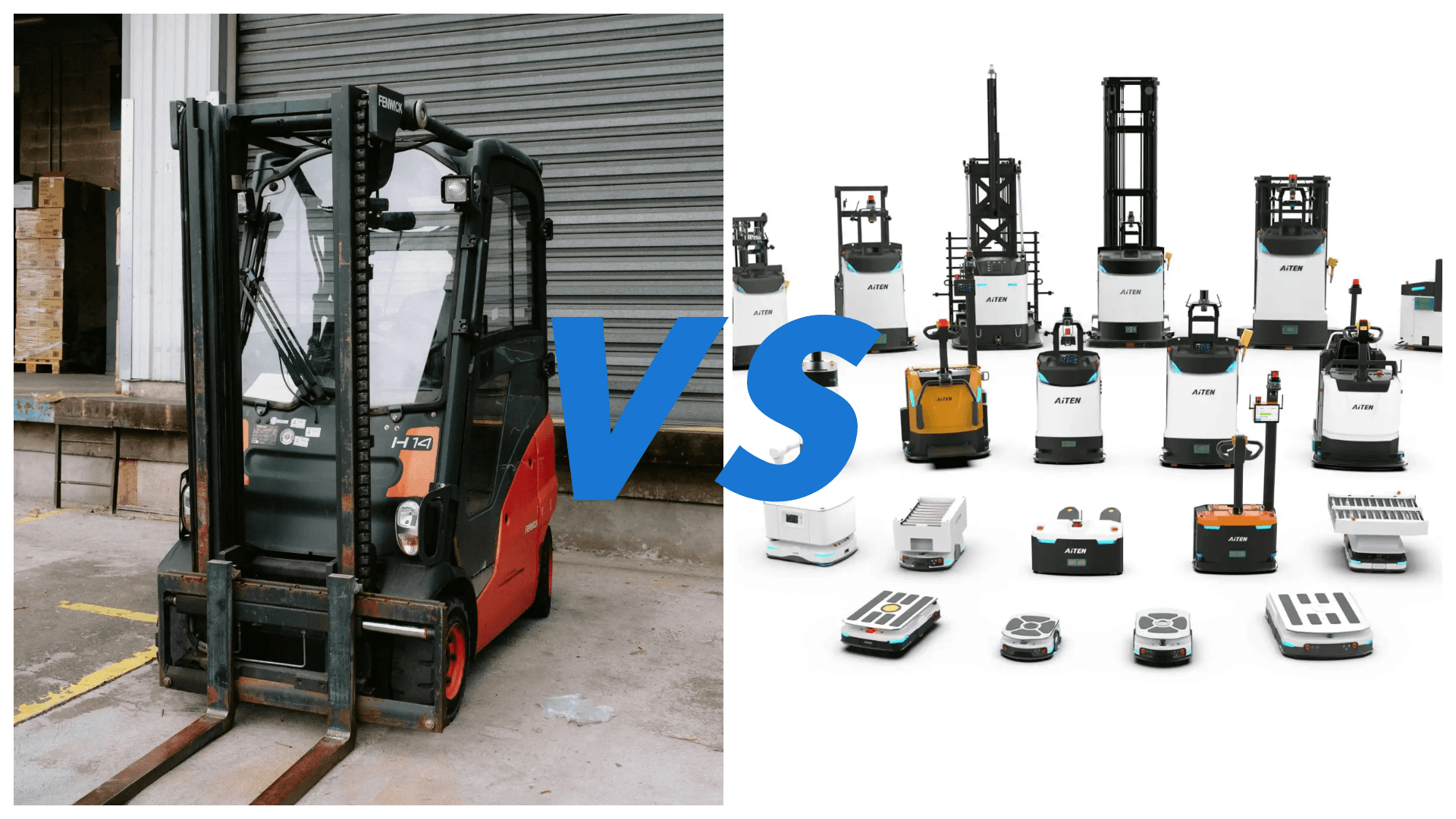
With the rapid development of intelligent logistics, unmanned forklifts have gradually become the ‘new favourite’ of the warehousing and manufacturing industries. Meanwhile, the traditional forklift, as the main force of industrial handling, is becoming increasingly distinct from them in terms of technology, functionality, and application scenarios. In this paper, we will comprehensively analyse the differences between unmanned forklifts and traditional forklifts from the dimensions of operation mode, safety, efficiency, cost, environmental adaptability, and other factors, providing a reference for enterprise selection.
1. Operation Mode: Automation vs Manual Dependency
Traditional forklift trucks are totally dependent on manual operation, and need to be driven and operated manually by professionally trained operators, who need to have appropriate driving skills and experience. Operators need to have appropriate driving skills and experience. Drivers need to manually control the driving, loading and unloading and stacking, and the whole operation process is completely controlled by manpower in real time, and the accuracy of the operation is limited by the personnel's experience and fatigue level.
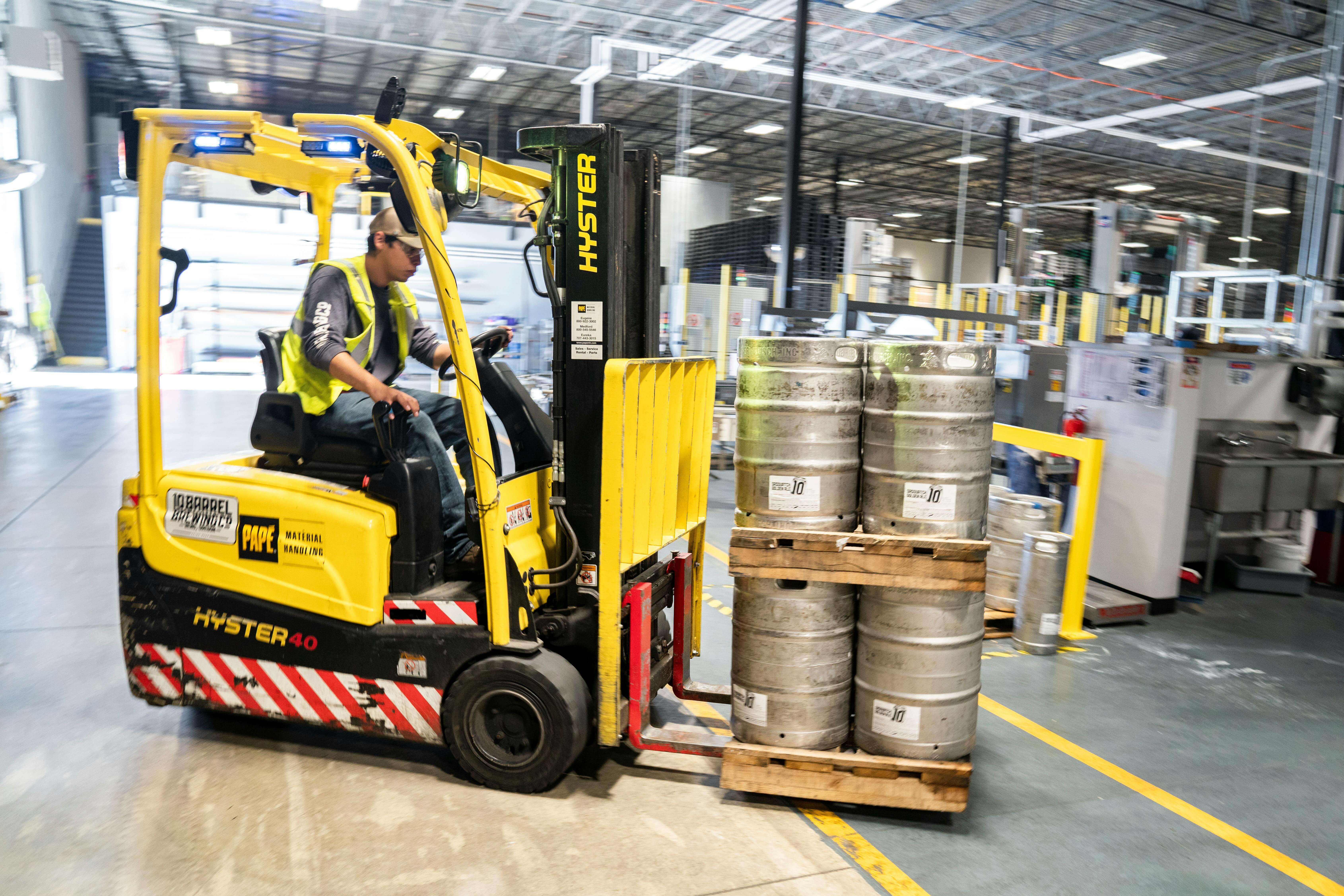
The unmanned forklift realises fully automated operation through advanced navigation technology, visual perception, AI algorithms and other technologies. It can automatically plan the travelling path according to the preset procedures and instructions, and complete the tasks of cargo handling and stacking, without the need for direct manual driving operation.
Core difference: Unmanned forklift trucks do not require human intervention and support 24-hour continuous operation, which significantly improves operational continuity.
For example, in a large logistics warehouse, when traditional forklift trucks are in operation, the driver needs to keep an eye on the surrounding environment and manually handle the goods; whereas unmanned forklift trucks, after the warehouse management system has issued a task, can travel from the starting point to the goods storage area on their own, accurately pick up the goods and carry them to the designated location, without human intervention in the whole process.
2. Safety: Multiple Protection vs Human Risk
The safety of traditional forklift operation depends largely on the driver's operating skills and attention. Although forklift trucks are equipped with some basic safety devices, such as horns, mirrors, etc., drivers are easily fatigued by long hours of operation, and may make mistakes in operation, which may lead to collision, cargo falling and other safety accidents. Traditional forklift accidents are frequent, with 100 deaths and 20,000 serious injuries caused by forklift accidents in the United States every year. Its safety risks mainly come from the driver's operating errors, blind spots and fatigue.
Unmanned forklift trucks are equipped with abundant and advanced safety protection systems. In addition to the common emergency contact safety device, automatic alarm device, emergency stop button device, but also equipped with object detectors, LIDAR, ultrasonic sensors, cameras and other sensors. These sensors are like the ‘eyes’ and ‘tentacles’ of the unmanned forklift, enabling it to sense the surrounding environment in real time. When obstacles or pedestrians appear on the travelling path, the unmanned forklift can automatically stop or actively avoid, greatly reducing the rate of accidents, safeguarding the safety of personnel and goods, and effectively reducing the uncertainty caused by manual operation.
- 360° Obstacle Avoidance: real-time detection of the environment, and automatic stopping or detouring in the event of obstacles;
- Precise Positioning: the fork repeatable loading accuracy reaches ±10mm, avoiding collision of goods;
- Emergency Button and Alarm Device: It can respond quickly to unexpected situations, reducing the rate of accidents.
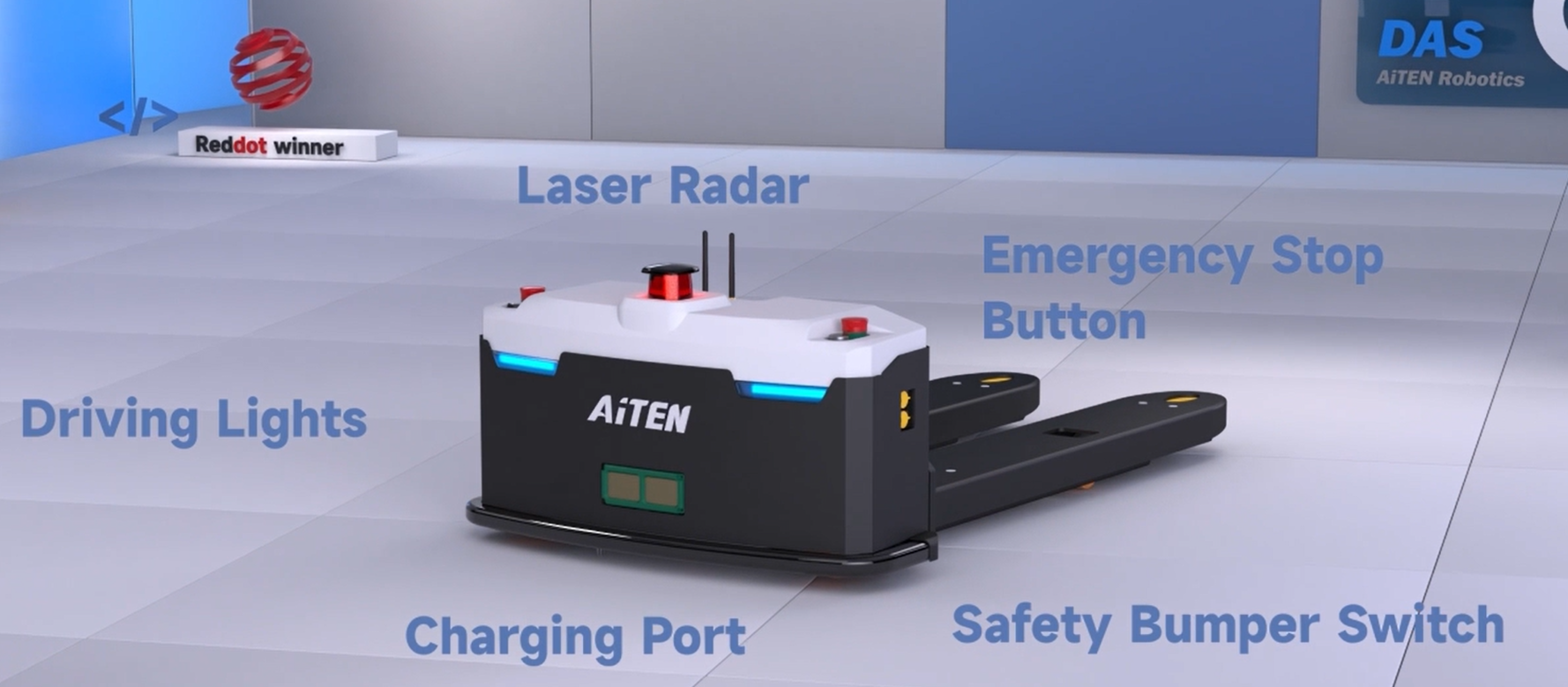
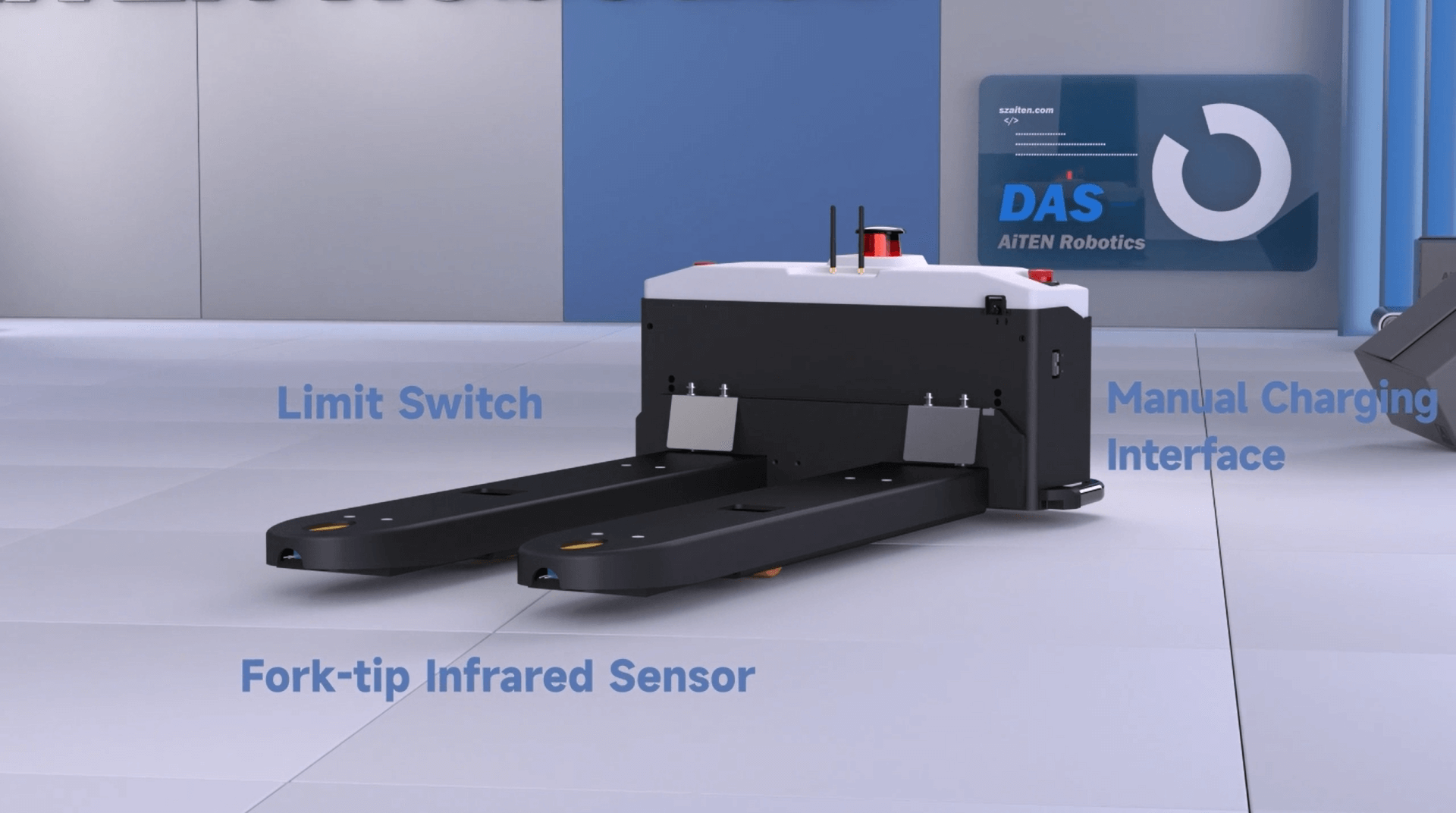
3. Efficiency and Cost: Long-term Benefits vs. Short-term Inputs
3.1. Efficiency Enhancement
The working hours of traditional forklift drivers are limited by legal regulations and human physiological limits, and they generally work limited hours per day. And they need to take a break after a period of consecutive work to maintain good working conditions, making it difficult for them to achieve round-the-clock efficient operation. During the working process, the driver needs time to start the forklift, adjust the driving posture and observe the surrounding environment when moving from one operation point to another, all of which will affect the overall operation efficiency.
The unmanned forklift can operate continuously 24 hours a day, and as long as there is sufficient electricity (or power source), it can operate tirelessly according to the set tasks and routes. At the same time, the unmanned forklift can realise multi-vehicle co-operation through an advanced scheduling system. In large-scale operation scenarios, multiple unmanned forklifts can travel at the same time, automatically avoid obstacles, and place goods in a precise and standardised manner, which greatly improves the operation efficiency and meets the automation, continuity and flexibilisation requirements of production. Through the intelligent scheduling system, the efficiency of unmanned forklift trucks is increased by more than 30% compared with traditional forklift trucks.
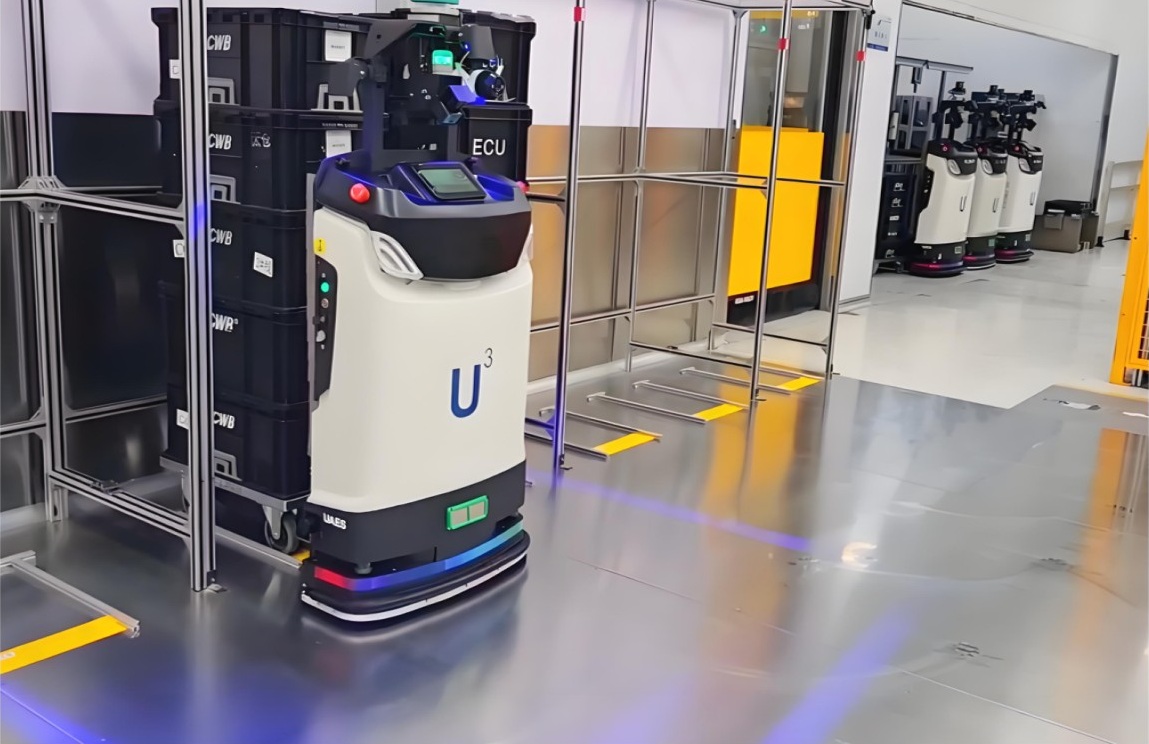
3.2. Cost Comparison
Traditional forklift operations require the employment of professional forklift drivers, and enterprises need to pay for the driver's wages, benefits, training costs and other labour costs. With the changes in the labour market, labour costs are rising year by year, which is a considerable expense for enterprises. In addition, the use of traditional forklift trucks also involves fuel (or charging) costs, regular maintenance and repair costs, parts replacement costs, etc.. Unmanned forklift trucks have a relatively high upfront procurement cost, but they do not require manual driving, which can significantly reduce the investment in manpower costs. Relevant data show that the application of unmanned forklifts can reduce warehouse costs by 30% and increase gross profit by 7%. Moreover, through the monitoring system, one person can achieve the scheduling and use of multiple forklifts, further saving manpower. At the same time, unmanned forklift trucks run at a stable pace, which reduces the loss of goods and equipment failure caused by human factors, and in the long run, the overall cost is lower.
- Initial cost: Traditional forklift trucks are low-priced (about tens of thousands of yuan), while laser-guided unmanned forklift trucks need hundreds of thousands of yuan.
- Long-term benefits: Unmanned forklift saves manpower costs (one person can dispatch multiple pieces of equipment), and 24-hour operation shortens the payback cycle (usually 1-2 years).
Example: Automotive Industry's Intralogistics Breakthrough! Automated Handling Saves 50% Costs
4. Environment Adaptability: Intelligent Response vs Scenario Limitations
Conventional forklift trucks have certain requirements on the working environment, which may affect the driver's operating comfort and equipment performance in cold and hot climatic conditions. In poor light or dusty, noisy environments, it will also affect the driver's vision and attention, thus affecting the safety and efficiency of the operation. For complex environments and narrow passages, there are certain limitations, and their functions and operation modes are relatively fixed and less adaptable.
Unmanned forklifts can easily adapt to different environments and sites, such as narrow passages, complex warehouse layouts, etc., and can be customised and transformed according to the needs, and can be seamlessly connected to other logistics equipment to realise automated production lines and logistics systems.
With sensor fusion and AI algorithms, unmanned forklifts can adapt to the following special scenarios:
- Dark environments: The unmanned forklift will not be affected by the use of the unmanned forklift in poorly lit environments. Dark environment: The unmanned forklift is not affected in poorly lit environments.
- Complex environment: The intelligent obstacle avoidance system and scheduling system can adapt to complex handling environments.
- Narrow space: it supports narrow aisle access and improves the utilisation rate of warehouse space.
Case: AiTEN Robot Narrow Aisle Handling Example
5. Maintenance and Management: Systematic O&M vs Traditional Maintenance
Traditional forklift maintenance is based on overhauling mechanical parts, while unmanned forklift needs to be combined with software upgrading, navigation calibration and data management. For example:
- Remote monitoring: real-time view of equipment status through the central control system, supporting fault warning and remote repair;
- Flexible upgrading: software algorithms can be iteratively optimised to adapt to dynamic business needs.
Conclusion: Future Trends of Unmanned Forklifts
Unmanned forklifts are reshaping the logistics industry with their advantages of automation, high safety and strong adaptability. Despite the high initial investment, its long-term cost reduction and efficiency value have been verified by many enterprises. In the future, with the deep integration of AI and 5G technologies, unmanned forklifts will evolve towards higher loads, lighter weight, and all-weather operations, becoming the core driving force of intelligent logistics.
If you have related unmanned forklift business needs, please contact us (AiTEN Robotics) and we will provide you with a free feasibility analysis based on your operation.