What Is an AGV Forklift? Working Principle, Applications & Comparison with AMRs
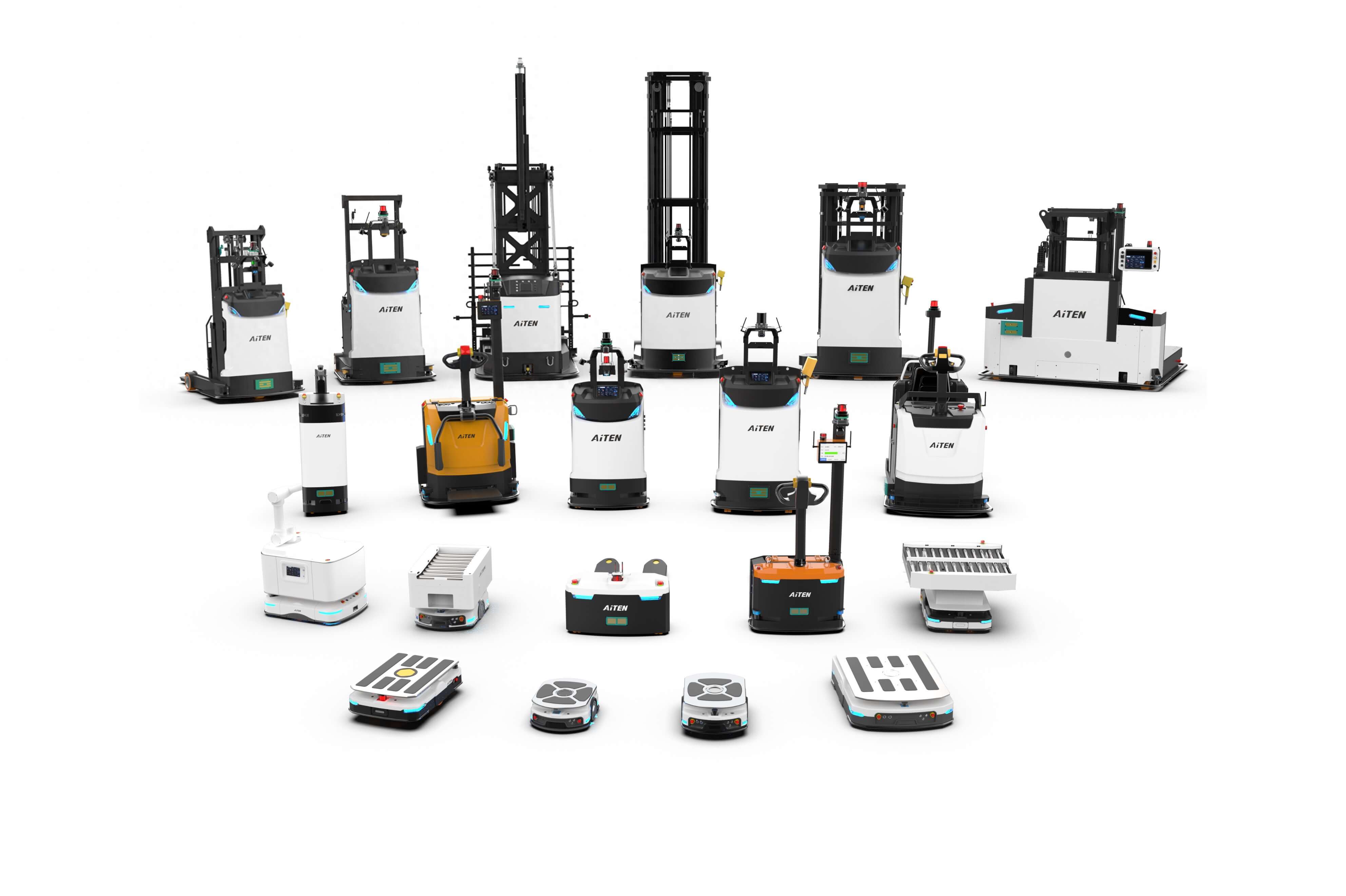
1. What Is an AGV Forklift?
An AGV forklift (Automated Guided Vehicle) is an automated material handling device that does not require manual operation. It combines the traditional forklift's cargo handling function with automated navigation technology, and is designed for industrial environments (e.g., warehouses, factories) to transport goods autonomously. It travels along a pre-set path through a navigation system (e.g. laser, magnetic stripe, vision sensors, etc.) to perform tasks such as pallet handling, stacking, loading and unloading, which improves efficiency, reduces labour costs and enhances safety.
2. The Working Principle of AGV Forklift Trucks
Navigation method
Traditional guidance technology, such as magnetic stripe navigation (relies on ground magnetic track), QR code navigation (needs to preset signs)
Modern technology: laser SLAM (build environment map by LiDAR), visual navigation (camera + AI algorithm)
Task execution: after receiving instructions from the scheduling system, it automatically plans the optimal path and combines with robotic arms or forks to complete the gripping, lifting and placing of goods, with an accuracy of up to ±10mm
3. What Is the Difference Between AGV and AMR?
AGV (Automated Guided Vehicle)
- Navigation: relies on fixed paths (e.g. magnetic stripes, guide rails)
- Infrastructure dependence: pre-laying of guidance facilities (e.g. magnetic stripes, reflective panels) is required.
- Obstacle avoidance capability: stops when encountering obstacles, requires manual intervention
- Flexibility: suitable for scenarios with high repeatability and fixed paths
- Cost: low initial cost, but high later path adjustment cost
- Applicable scenarios: high loads (up to several tonnes), long-distance fixed route transportation
- Typical application: Suitable for fixed route material transport (e.g. production line, warehouse pallet handling).
AMR (Autonomous Mobile Robot)
- Navigation: dynamic path planning through sensors, AI and SLAM technology, adaptable to dynamic environments
- Infrastructure dependence: no need for physical guidance, free navigation through software maps
- Obstacle avoidance: Autonomous bypassing of obstacles, real-time path adjustment
- Flexibility: adapts to dynamic environments, tasks and routes can be adjusted at any time
- Cost: high initial cost, but long-term flexibility
- Scenarios: lightweight (typically <1 tonne), complex and variable small batch handling
- Typical applications: for dynamic tasks (e.g. picking in warehouses with changing layouts, distribution in mixed human-machine environments)
However, there has been a trend towards the convergence of AGV and AMR technologies, for example, AiTEN Robotics AGVs can also dynamically plan their paths with sensors, AI and SLAM technologies.
For more information: What Is the Key Difference Between AMR and AGV?
4. Application Scenarios of AGV Forklifts
Warehouse logistics: pallet handling, shelf replenishment, cross-regional transport and conveyor line connection.
Manufacturing workshop: automatic distribution of production line materials, finished goods into the warehouse
Special scenarios: hazardous environments (e.g. chemical warehouses), high-precision operations (e.g. pharmaceutical cold chain), low-temperature environment to replace manual labour (e.g. cold storage).
AiTEN Robot Case:
.jpeg)
5. Advantages of AGV Forklifts
Efficient continuous operation: 24 hours of uninterrupted operation, no manual fatigue problem.
Accuracy: Reduce human error in operation and improve the accuracy of inventory management.
Safety: Equipped with laser obstacle avoidance and emergency stop device to reduce the accident rate.
Integrability: linked with WMS (Warehouse Management System), ERP (Enterprise Resource Planning) and other systems to achieve intelligent scheduling.
For more information: What Are the Advantages of Using an Autonomous Forklift?
Summary
AGV forklifts significantly improve logistics efficiency through automation technology, while AMR is more suitable for flexible and dynamic environments. The choice between the two needs to be based on specific scenarios: AGVs are preferred if stability and large loads are pursued; AMRs are more advantageous if complex environments need to be adapted and infrastructure modifications need to be minimised.
If you want to explore solutions for your smart factory, please contact us, and we will provide you with free feasibility analysis based on your operational situation.