How Do Automated Forklifts Work? The Future of Material Handling
.MP10S%E5%8A%A0%E9%AB%98%E6%94%AF%E6%9E%B6%20(3).png)
Automated forklifts, also known as Autonomous Guided Vehicles (AGVs) or Autonomous Mobile Robots (AMRs), are revolutionising material handling by combining robotics, sensors, and artificial intelligence (AI) to perform tasks without human intervention, especially in the context of smart factories and modern warehouses. Understanding how they work can provide insights into their growing significance in the industrial landscape. Here's a detailed explanation of how they work:
1. Core Components of an Automated Forklift Truck
a. Navigation System
- Laser SLAM (Simultaneous Localization and Mapping): Uses LiDAR sensors to create a real-time map of the environment and locate itself within it. The forklift's on-board computer then uses this map to calculate the best route to reach a destination. This type of navigation is highly flexible as the forklift can adapt to changes in the environment.
- Vision Navigation: Vision-guided navigation relies on the cameras installed on the forklift. The cameras capture images of the environment, and computer vision algorithms analyse these images to identify landmarks, signs, and other visual cues. This method is highly adaptable and does not require any physical infrastructure such as magnetic tapes. It can also be used in combination with other navigation methods, such as laser-based navigation, for enhanced accuracy.
- Magnetic Tape Guidance: A magnetic tape is laid on the floor of the factory or warehouse, following the desired paths for the forklift. The forklift is equipped with a sensor that detects the magnetic field of the tape. As the forklift moves, it follows the magnetic signal, staying on the pre-defined route (older systems). It lacks flexibility as any changes to the route require physically re-laying the magnetic tape.
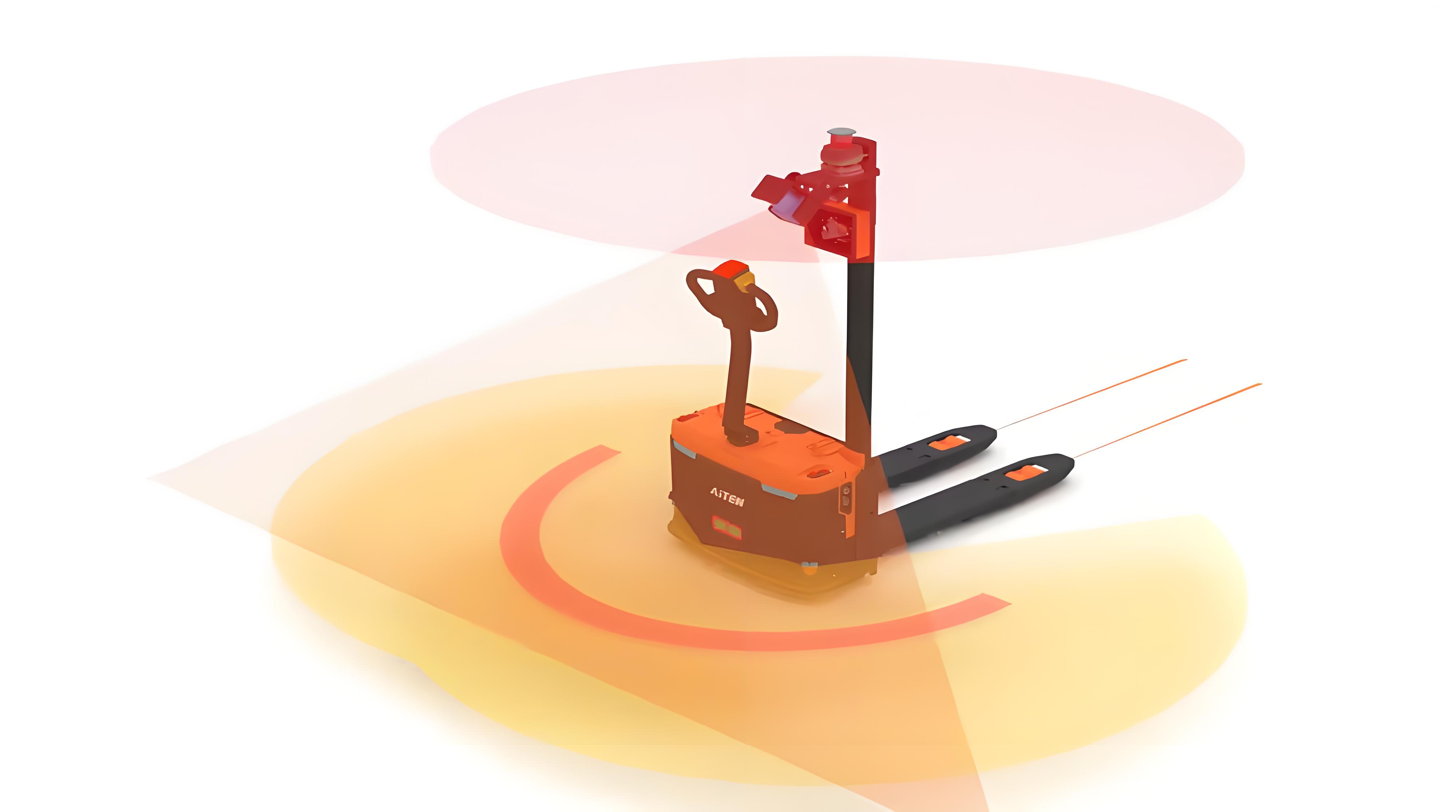
b. Sensors
- 3D LiDAR (Light Detection and Ranging): LiDAR is a fundamental sensor in automated forklifts. It emits laser light pulses and measures the time it takes for the light to bounce back from surrounding objects. By doing so, it creates a detailed 3D map of the forklift's environment. This real-time mapping is crucial for navigation, allowing the forklift to detect obstacles, other vehicles, and the layout of the facility. For example, in a busy warehouse, the LiDAR sensor can quickly identify the location of pallets, racks, and any workers in the vicinity, enabling the forklift to plan its route accordingly.
- Ultrasonic/Infrared Sensors: Provide short-range obstacle detection (0.1–3 meters).ultrasonic sensors, a type of proximity sensor, work by emitting high-frequency sound waves and measuring the time it takes for the waves to bounce back. These sensors are especially effective in detecting small or irregularly shaped objects that might be missed by other sensors. For instance, an ultrasonic sensor can detect a small tool left on the floor in the forklift's path, preventing a potential collision.
- IMU (Inertial Measurement Unit): Ensures stability on uneven floors.
c.Control System
- On-board Computers: Automated forklifts are equipped with powerful on-board computers. These computers are responsible for processing the data from all the sensors, making decisions based on that data, and controlling the movement of the forklift. They run complex software algorithms that are designed to optimize the forklift's performance. For example, the on-board computer can calculate the most efficient route to a destination based on factors such as the distance, the presence of obstacles, and the battery level. It also controls the speed, acceleration, and deceleration of the forklift, ensuring smooth and safe operation.
- Connectivity and Communication: Automated forklifts need to communicate with other systems in the factory or warehouse. They use wireless communication technologies such as Wi - Fi or Bluetooth to connect to the facility's network. This allows them to receive instructions from a central control system, such as a warehouse management system (WMS). For example, when a new order is received in the WMS, it can send instructions to the nearest available automated forklift, telling it where to pick up the required goods and where to deliver them. The forklift can also send back data to the WMS, such as its location, the status of the load it is carrying, and any error messages. This two-way communication is essential for coordinating the activities of multiple automated forklifts in a busy industrial environment.
- Fleet Management Software: Coordinates multiple forklifts (e.g., AiTEN RDS system).
d. Power System
- Battery-Powered (Lithium-ion/Lead-Acid): 6–8 hours of runtime, 2 hours fast charging.Provides power for extended operation.
2. How Automated Forklifts Work: Step-by-Step
Step 1: Task Assignment
- Input: A warehouse management system (WMS) sends a task (e.g., "Move pallet from Zone A to Zone B").
- Priority Handling: The system assigns tasks based on urgency and forklift availability.
Step 2: Path Planning
- Dynamic Routing: Avoids collisions and traffic jams using real-time data.
- Example: If Forklift #1 is blocked, the system reroutes Forklift #2.
Step 3: Pallet Handling
- Fork Adjustment: Auto-adjusts fork height/width based on pallet size (vision-guided).
- Load Verification: Weight sensors confirm safe lifting (e.g., ≤1,500 kg).
Step 4: Obstacle Avoidance
- Emergency Stop: Halts if a human enters safety zone.
- Detour: Recalculates path if blocked (response time: <0.5 seconds).
Step 5: Delivery & Reporting
- Precision Placement: Lowers pallet within ±10mm accuracy.
- Data Sync: Updates inventory in WMS and logs performance metrics (e.g., cycle time).
3. Key Technologies Driving Automation
AI Vision
- Role: Identifies pallets, detects damage, and reads barcodes.
- Example: AiTEN’s Vision-guided AGV
5G Connectivity
- Role: Enables real-time communication in large warehouses.
- Example: AiTEN’s 5G-enabled Forklifts
Digital Twin
- Role: Simulates workflows to optimize routes and predict failures.
- Example: AiTEN’ AGV Digital Twin Platform
4. Advantages Over Manual Forklifts
- Cost Savings: Reduce labor costs by 30–50% (no shifts or breaks).
- Safety: Eliminate 80% of workplace accidents caused by human error.
- Efficiency: Operate 24/7, achieving 200+ pallet moves/day per forklift.
.MP10S%E5%8A%A0%E9%AB%98%E6%94%AF%E6%9E%B6%20(3).png)
5. Applications Across Industries
- E-commerce: Sorting multiple items at an e-commerce company's distribution centre.
- Automotive: Ship car batteries and parts with 99.99% accuracy.
- Pharmaceutical: Handling sterile goods in a temperature-controlled environment.
In conclusion, automated forklifts are sophisticated machines that combine sensors, navigation systems, and control systems to perform material handling tasks autonomously. Their ability to work efficiently, safely, and in coordination with other systems makes them an invaluable asset in modern industrial settings. As technology continues to advance, we can expect automated forklifts to become even more intelligent and capable, further transforming the way materials are moved and managed in factories and warehouses.
For more insights on autonomous forklifts and smart warehouse solutions, stay tuned to our blog! Ready to explore solutions? Contact us for a free feasibility analysis tailored to your operations.