Handling Robot Internals Explained: How the AiTEN MP10S Robot Operates Efficiently
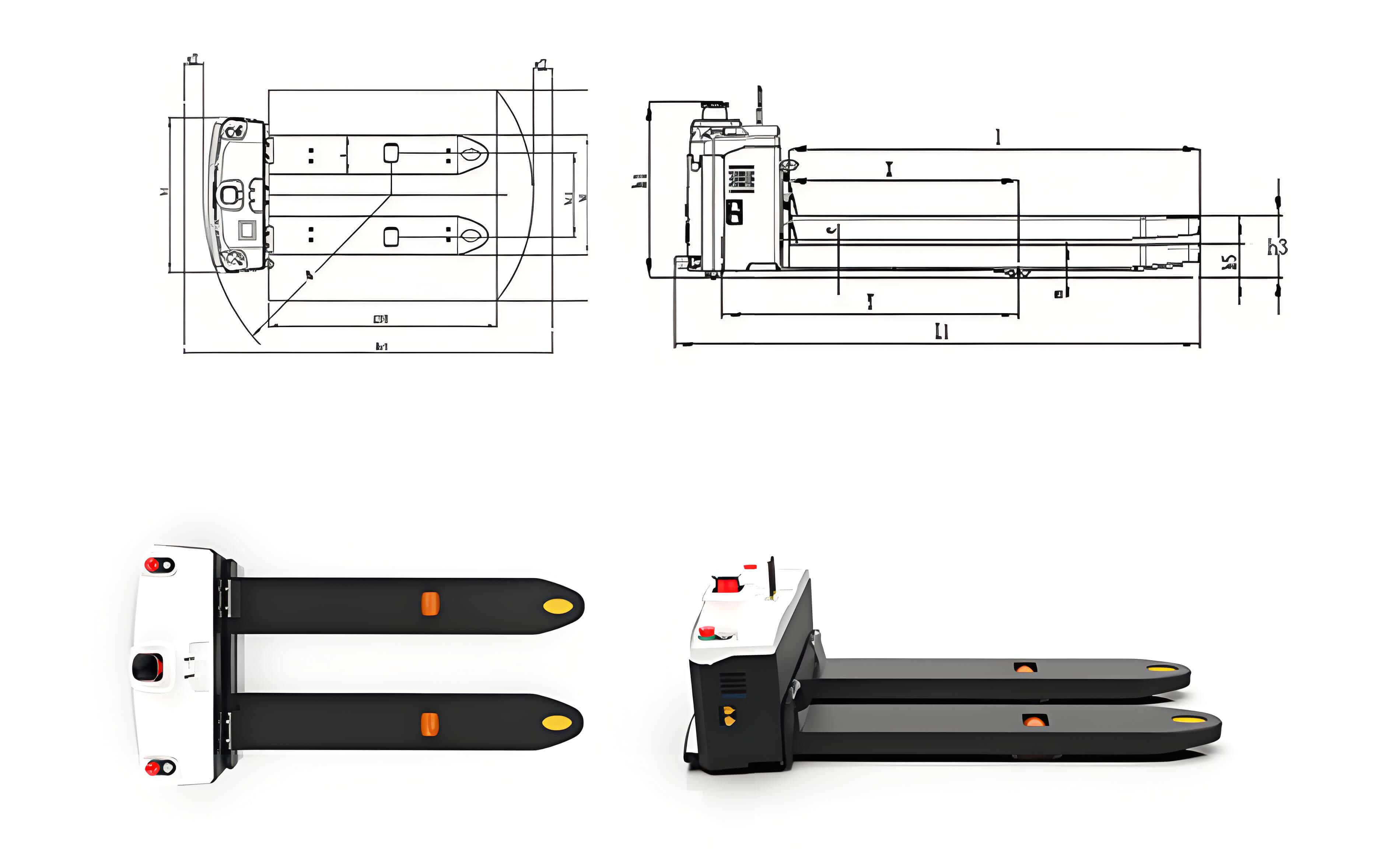
From control systems to 3D SLAM navigation, read how handling robots work and their core components in one article.
Are you curious about how the handling robots that travel freely in factories work? Handling robots are automated devices used to transport and transfer materials in factories or other environments. As the core equipment of intelligent logistics, handling robots have become the industry standard for precise navigation and efficient collaboration. In this article, we take the red dot award-winning AiTEN MP10s as an example, and analyse the five core systems of handling robots in depth, reveal their internal structure and operating principles, and understand the secrets of handling robots!
1. The ‘Heart’ of a Handling Robot: the Control System
For a handling robot, the control system is its heart. The core of this system is an industrial computer or PLC (built-in logic controller), which is responsible for receiving tasks, planning paths, and giving commands, so that the robot can efficiently carry out the handling work.
MP10S integrates with enterprise WMS and MES systems to achieve automatic task assignment and scheduling, while supporting real-time path planning and collaborative work of multiple robots to avoid congestion and conflicts and improve overall work efficiency.
It is worth mentioning that AiTEN had launched its own fully self-developed controller - AiTEN RC-F3.0 Core AI Brain, which deeply integrates with the system to achieve seamless connectivity and significantly improve the stability and co-ordination of vehicle operation. It is a master controller chip designed specifically for motorised industrial vehicles, with surging computing power, broad compatibility, flexible adaptation to various types of vehicles, accelerating the deployment process, taking into account the maximisation of cost-effectiveness.
2. The ‘Limbs’ of a Handling Robot: Drive System
The action of the handling robot relies on the drive system, just like human legs, which determines how the handling robot moves, and the common drive modes are single rudder wheel drive, double rudder wheel type, differential wheel type and McNamee wheel type.
MP10S adopts differential drive + emergency power-off design, which is highly flexible and responds quickly to braking in unexpected situations to ensure the safety of human-machine mixing.
3. The ‘Eyes’ of the Handling Robot: the Navigation System
If a handling robot does not have eyes, it is like walking blindfolded and may hit the wall at any time. Therefore, the navigation system is the key technology that determines whether a handling robot can accurately reach its target.
MP10s adopts 3D SLAM laser navigation technology, which can ensure its precise positioning and autonomous route planning in the complex and changing warehouse environment, with a positioning accuracy of ±10mm. 3D SLAM laser navigation technology analysis (MP10s core configuration):
- Real-time construction of three-dimensional environment map, positioning accuracy of ± 10 mm
- Dynamic obstacle avoidance algorithm, adapting to shelf changes/personnel flow scenarios
- Supports non-marking operation, reducing deployment costs
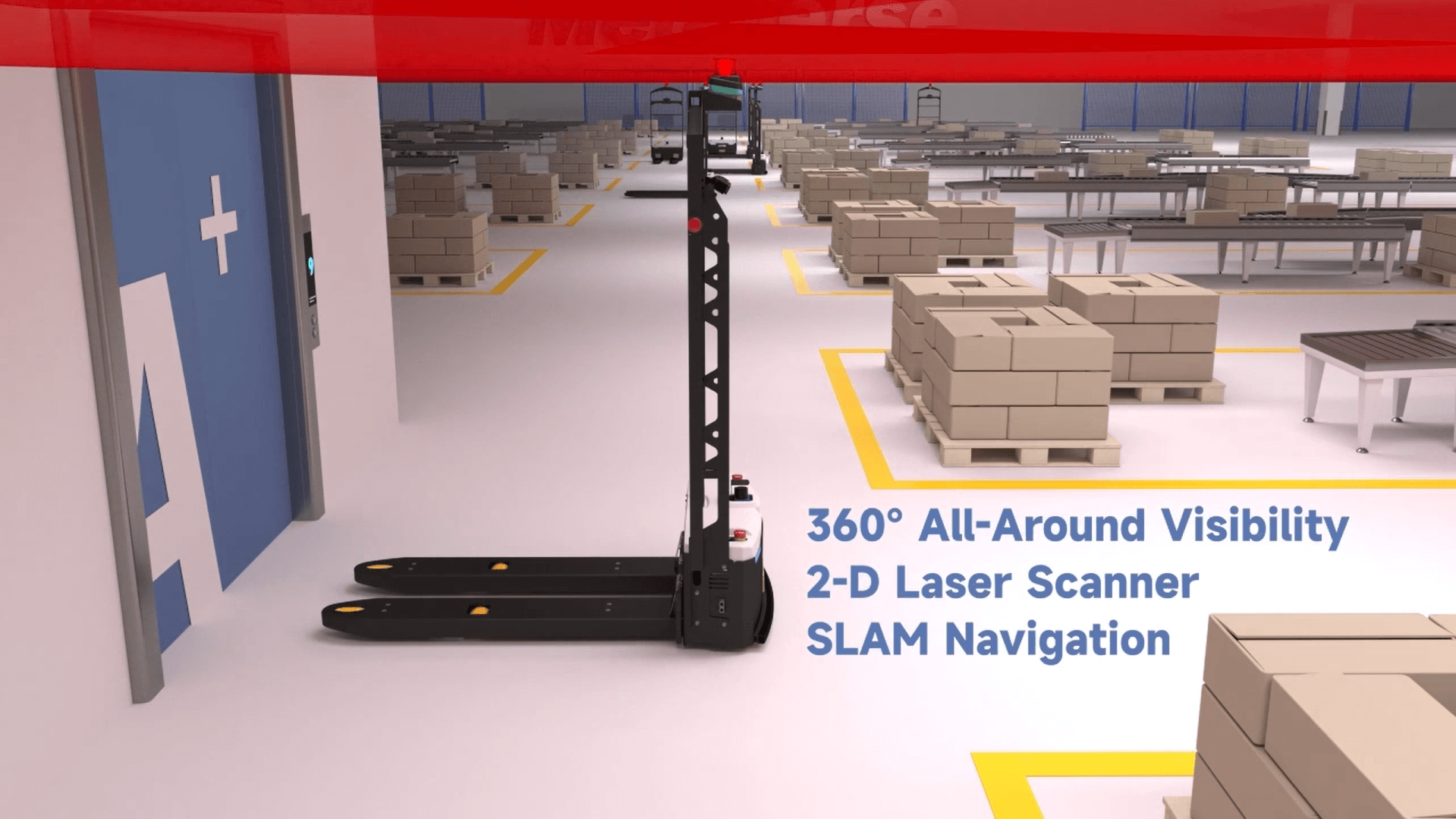
At present, the mainstream navigation methods on the market also include magnetic stripe navigation, two-dimensional code navigation, visual navigation, etc. Different navigation methods are suitable for different work scenarios. Magnetic stripe navigation is suitable for fixed routes between warehouse shelves, laser navigation is suitable for complex scenarios, visual navigation uses cameras to identify ground markers or environmental features, which is more flexible, and SLAM navigation is more suitable for dynamically changing environments.
4. The ‘Sensing Nerve’ of a Handling Robot: the Sensor System
The handling robot needs to notice obstacles and recognise the environment during operation, which requires a variety of sensors to collect information. It can be said that the sensors are like the nervous system of the handling robot, which can ‘see’, ‘hear’ and ‘sense’ the changes around it.
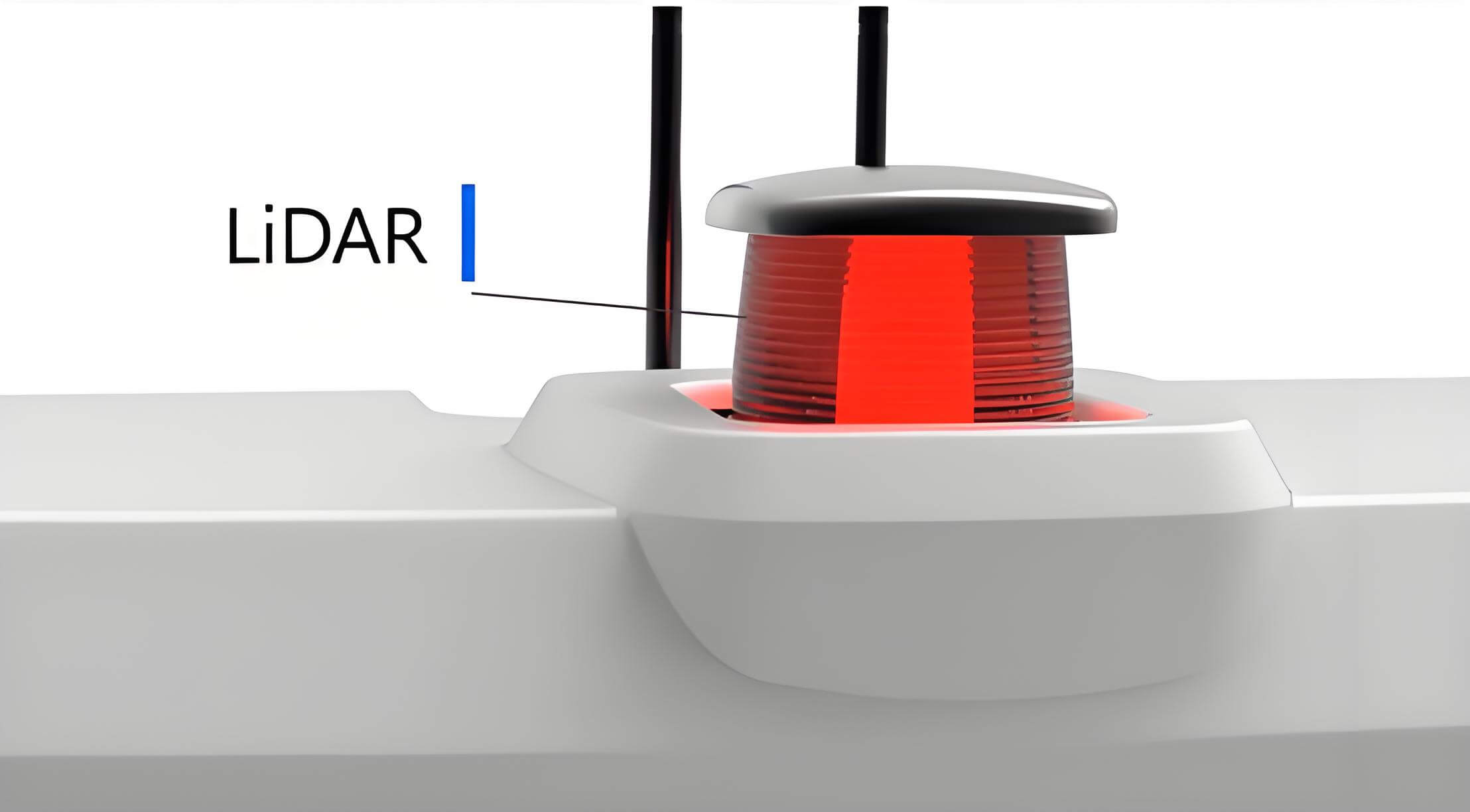
LIDAR is a commonly used sensor for handling robots, which can detect obstacles and perform autonomous obstacle avoidance.
The fork-tip sensor and the goods-in-place sensor are coordinated to control the accuracy within ±10 mm.
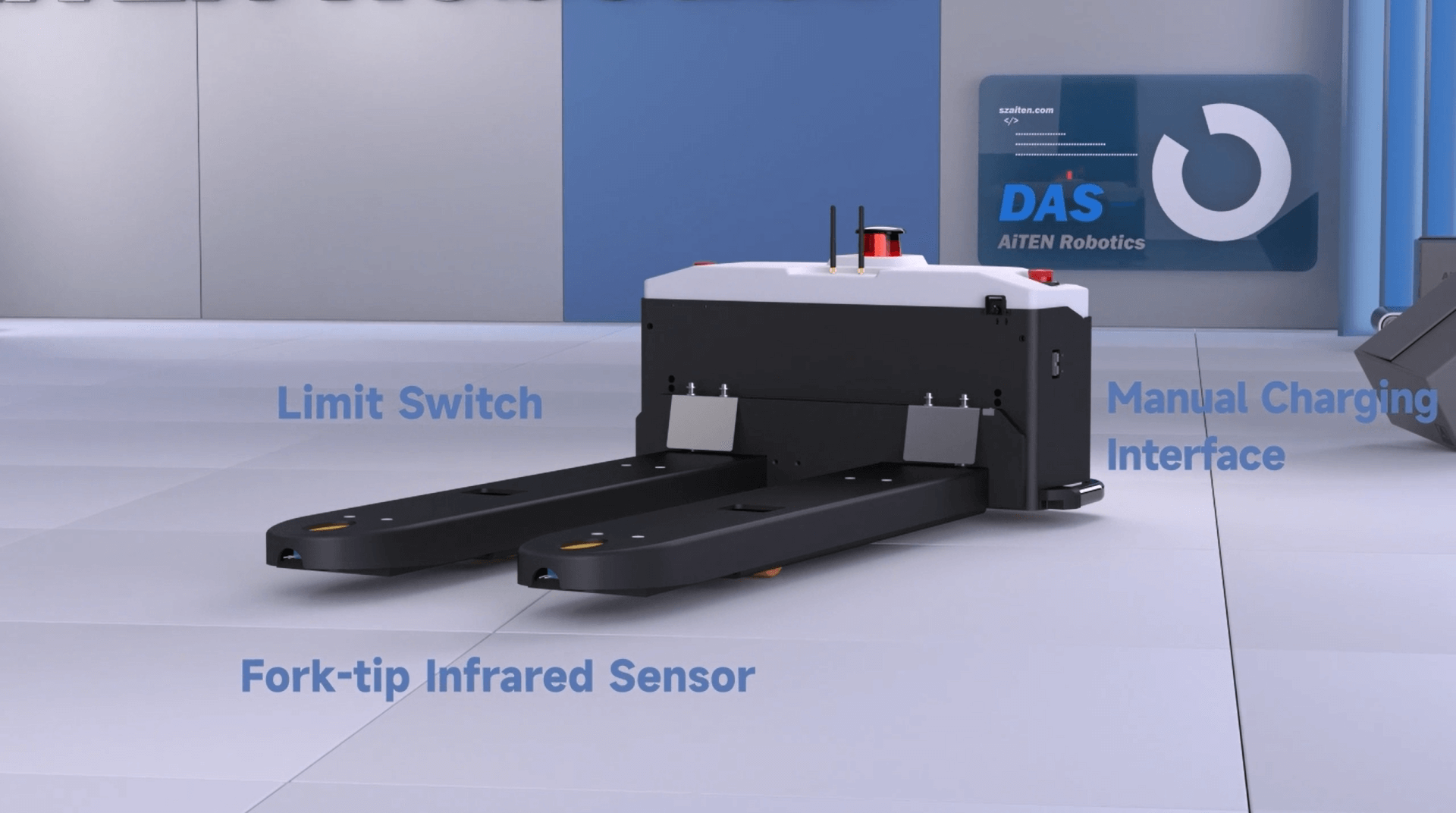
With these sensors, the handling robot is not only able to accurately follow the route and carry the goods, but also able to sense the surrounding environment in real time, avoiding collision accidents and improving operational safety.
AiTEN's MP10S handling robot has passed CE certification and is equipped with audible and visual alarms and an emergency stop button, realising triple safety protection for people, machines and goods.
5. The ‘Energy Source’ of Handling Robots: Batteries and Charging Systems
No matter how powerful a handling robot is, it will remain motionless without electricity. Commonly used batteries for handling robots are lead-acid batteries, lithium batteries and supercapacitors. Lead-acid batteries have low cost but long charging time; lithium batteries have high energy density, long service life and support fast charging, but at a higher cost; supercapacitor has a fast charging speed but the endurance time is terminated, which is suitable for high-frequency and short-distance operation.
MP10S adopts lithium iron phosphate battery, with high safety and security, rated operating range of 6~8 h, charge and discharge cycle times up to 2000 times, support fast charging, charging time <1 h.
In order to improve work efficiency, many handling robots are equipped with automatic charging function, when the power is insufficient, they will automatically arrive at the charging station to replenish the energy to ensure that the short time operation, MP10S is no exception.
Summary
Introduced here, the structure of the handling robot is also clear enough, mainly composed of the following core parts:
- Control system: responsible for commanding the handling robot to perform the task and plan the path.
- Drive system: decides how the handling robot moves and chooses the appropriate drive mode.
- Navigation system: enables the handling robot to reach the target accurately and will not get lost.
- Sensor system: helps the handling robot to sense the surrounding environment, avoid obstacles and prevent collision.
- Battery and charging system: provide power, support automatic charging, improve the endurance.
If you want to know more models and functions of handling robots, please contact us (AiTEN Robotics), we will provide you with free feasibility analysis according to your operation.