From Heavy Lifting to Intelligent Logistics: The Evolution of Handling Robots
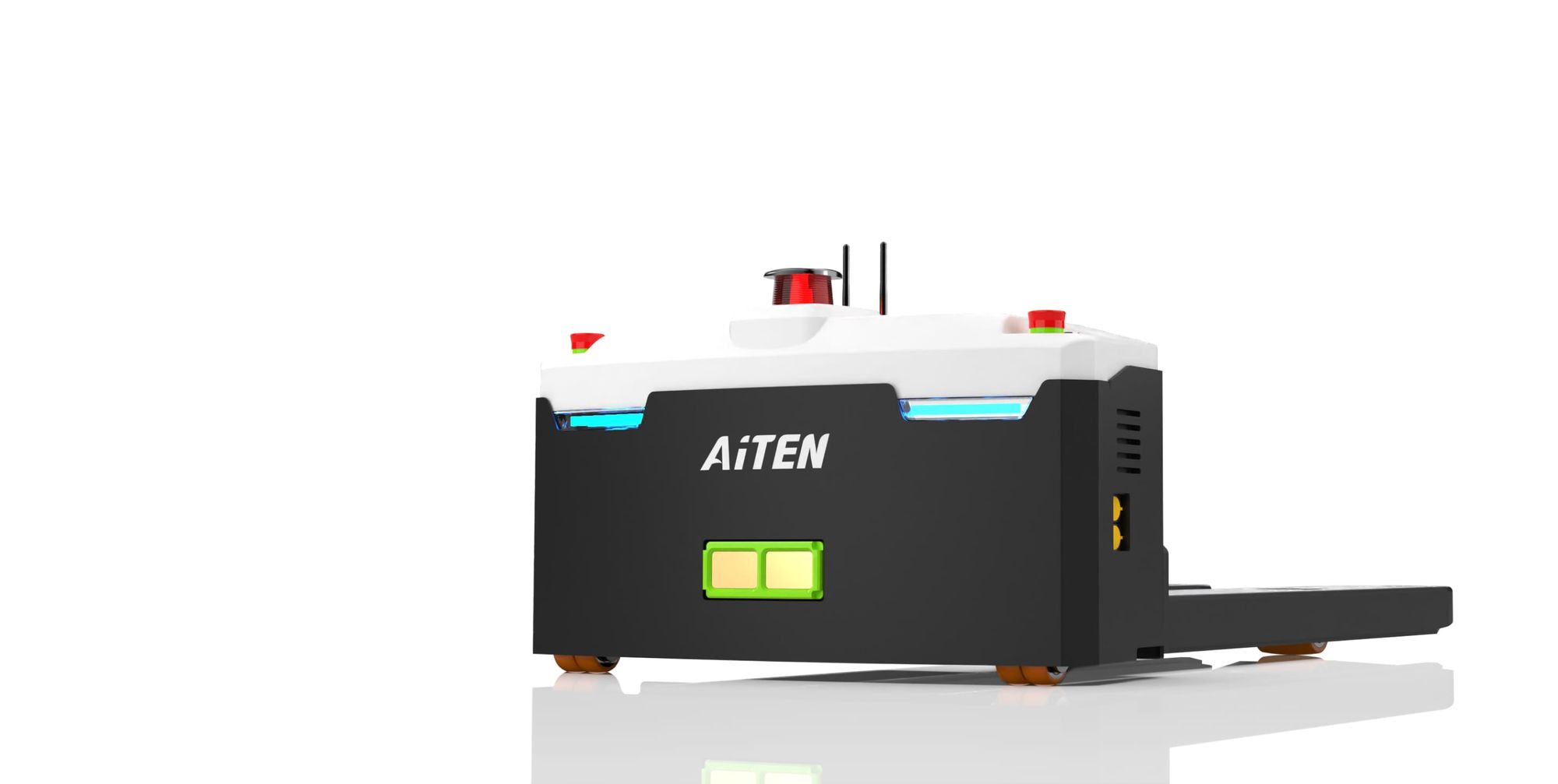
Introduction of Handling Robots
Handling robots, as the name suggests, are industrial robots that can carry out automated handling operations.
As an important part of industrial automation, handling robots have evolved from simple to complex, from single function to multi-function. 1960, Versatran and Unimate robots were used for handling operations in the United States, which marked the official birth of handling robots. These early robots were mainly used for simple and repetitive tasks, such as lifting and moving heavy loads or performing basic assembly operations. These early robots were used for simple repetitive tasks such as lifting heavy objects or performing basic assembly operations.
In the 1970s and 1990s, with advances in computer technology and control systems, handling robots were able to adapt to more complex environments and tasks, and began to develop in the direction of intelligence, beginning to have a certain degree of autonomous decision-making capabilities, such as path planning and dynamic obstacle avoidance.
Into the 21st century, handling robots ushered in the golden age of intelligent development, capable of achieving higher precision positioning and navigation, and is widely used in warehousing, manufacturing, medical, logistics and other fields.
What Are the Three Main Parts of the Handling Robot
The core of the handling robot is mainly composed of three parts: drive system, navigation system and control system.
- The drive system, including motors, wheel sets, etc., is responsible for the robot's movement and load capacity.
- The navigation system, such as LiDAR, vision sensors, etc., is used to achieve the robot's positioning and path planning.
- The control system, which integrates AI algorithms, is responsible for coordinating task scheduling, obstacle avoidance and data interaction.
What Are the Types of Handling Robots?
According to the different technology paths and application scenarios, handling robots are mainly divided into the following types.
The first one is AGV (Automated Guided Vehicle), this kind of robot runs on a fixed route by magnetic stripe, 2D code or laser navigation, which is suitable for high-precision handling scenarios.AiTEN MP10 is a typical AVG handling robot, which can work flexibly in narrow space by using the advanced navigation technology, with the positioning accuracy up to ±10mm. It is small, flexible and versatile.
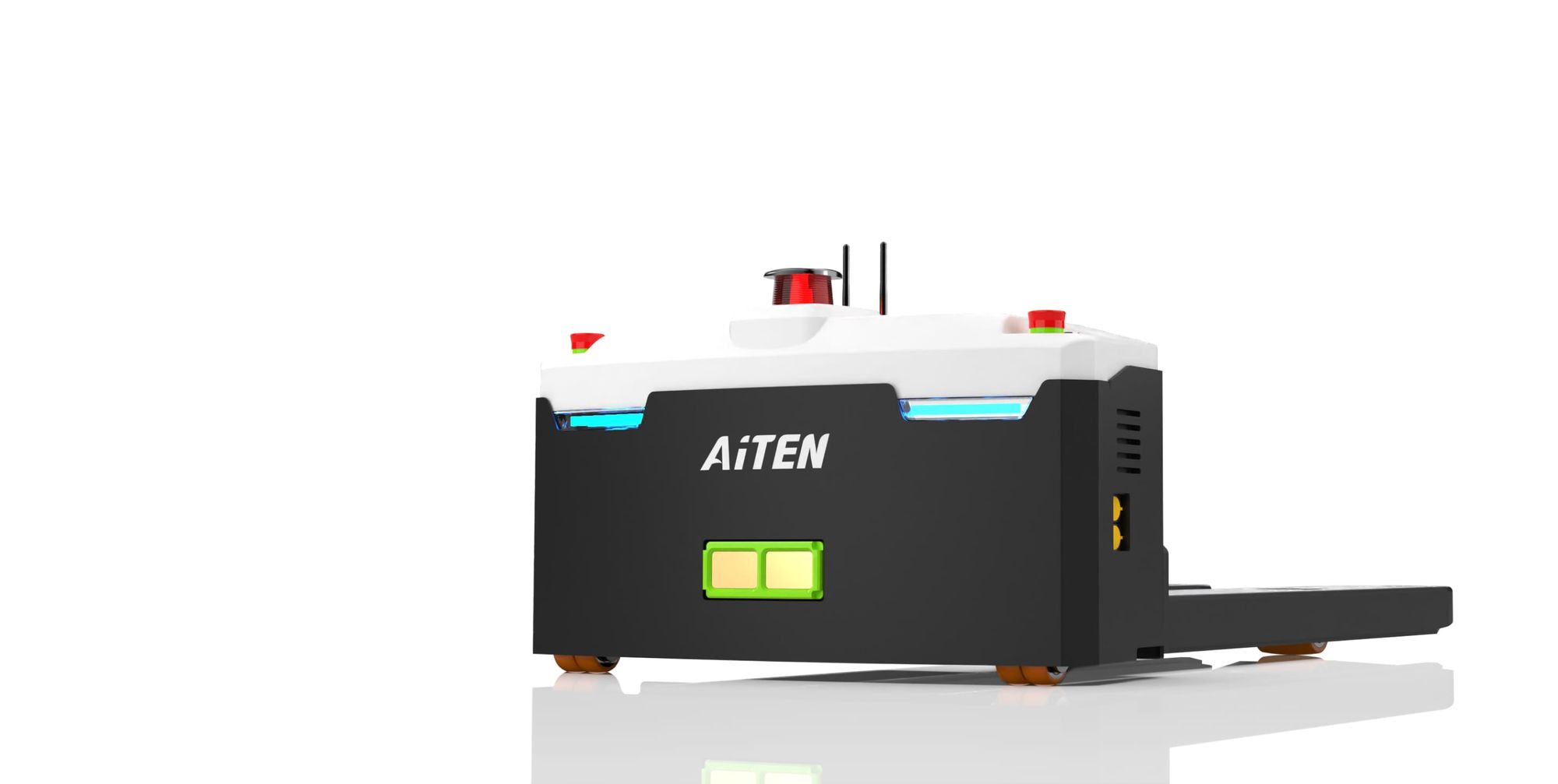
Next is AMR (Autonomous Mobile Robot), which is based on SLAM technology to achieve autonomous navigation, higher flexibility, dynamic obstacle avoidance, suitable for complex and changing environments. For example, AiTEN's TP100 is a typical AMR, which adopts a dual-LIDAR fusion navigation system with an accuracy of up to ±5mm and a 360° safe obstacle avoidance capability.

In addition, there are handling robotic arms and other types, combining a robotic arm with a mobile chassis, capable of realising integrated gripping and handling operations.
With the continuous progress of technology, handling robots are developing towards higher intelligence and wider application scenarios. Whether it is AGV or AMR, or other types of handling robots, they are providing strong support for the upgrade of industrial automation and intelligent logistics.
For more insights on handling robots, stay tuned to our blog! Ready to explore solutions? Contact us for a free feasibility analysis based on your operation.