AiTEN Material Handling Robot in Textile Machinery Manufacturing Application Case
The enterprise is a core solution provider in the field of chemical fibre production, providing full-process equipment and polycondensation/extrusion systems covering man-made fibre spinning, stretching machines, BCF carpet yarn, etc., supporting the complete production chain from monomers to finished products, as well as complementary engineering services and intelligent digital solutions to promote industrial upgrading.
Industry Pain Points
In the pursuit of efficient production of textile machinery workshop, these logistics bottlenecks are eating up your profits:
1. Difficulty in Passing Through the Aisle
The large turning radius of traditional forklift trucks material accumulation leads to production line stagnation.
2. High Safety Hazard
The average daily interaction between people and vehicles is more than 200 times, and the risk of work injury is caused by sudden emergency stops and visual blindness.
3. Difficulty in Data Tracking
Tens of thousands of handling actions per month, but can not track the time, path deviation, equipment utilisation and other key indicators.
4. Long-Distance Energy Consumption
The average daily handling kilometres in the factory, labour costs and energy costs double.
APe15 Material Handling Robot: Breaking Through Four Bottlenecks with Hardcore Technology
As an international standard setter for textile machinery, the enterprise integrates the intelligent logistics system into the whole production chain:
1. Narrow-Aisle Handling
√ 1.2-metre ultra-narrow body specially designed for textile machinery workshops, easily traversing 1.8-metre aisles.
√ Load capacity of 1.5 tonnes, to meet the textile machinery parts and other heavy materials handling
2. Safety in All Areas
√ 360° LIDAR + 3D vision obstacle avoidance, real-time detection of pedestrians and low obstacles.
√ CE-certified safety architecture, quick response time for emergency stops.
3. Data Empowerment
√ RDS scheduling system + LMS logistics management system, real-time monitoring of handling time, path optimisation rate
√ Automatic generation of data analysis reports helps lean management
4. Ultra-Long Battery Life
√ Lithium iron phosphate battery supports 2 hours fast charging, 6-8 hours of continuous operation.
√ 40% lower energy consumption than traditional diesel forklifts.
Intelligent Handling Revolution from Command to Closed Loop
‘Intelligent Logistics System’ realises fully automated operations:
1. Task Trigger
The system sends out tasks with one click, and the tablet PC receives instructions in real time.
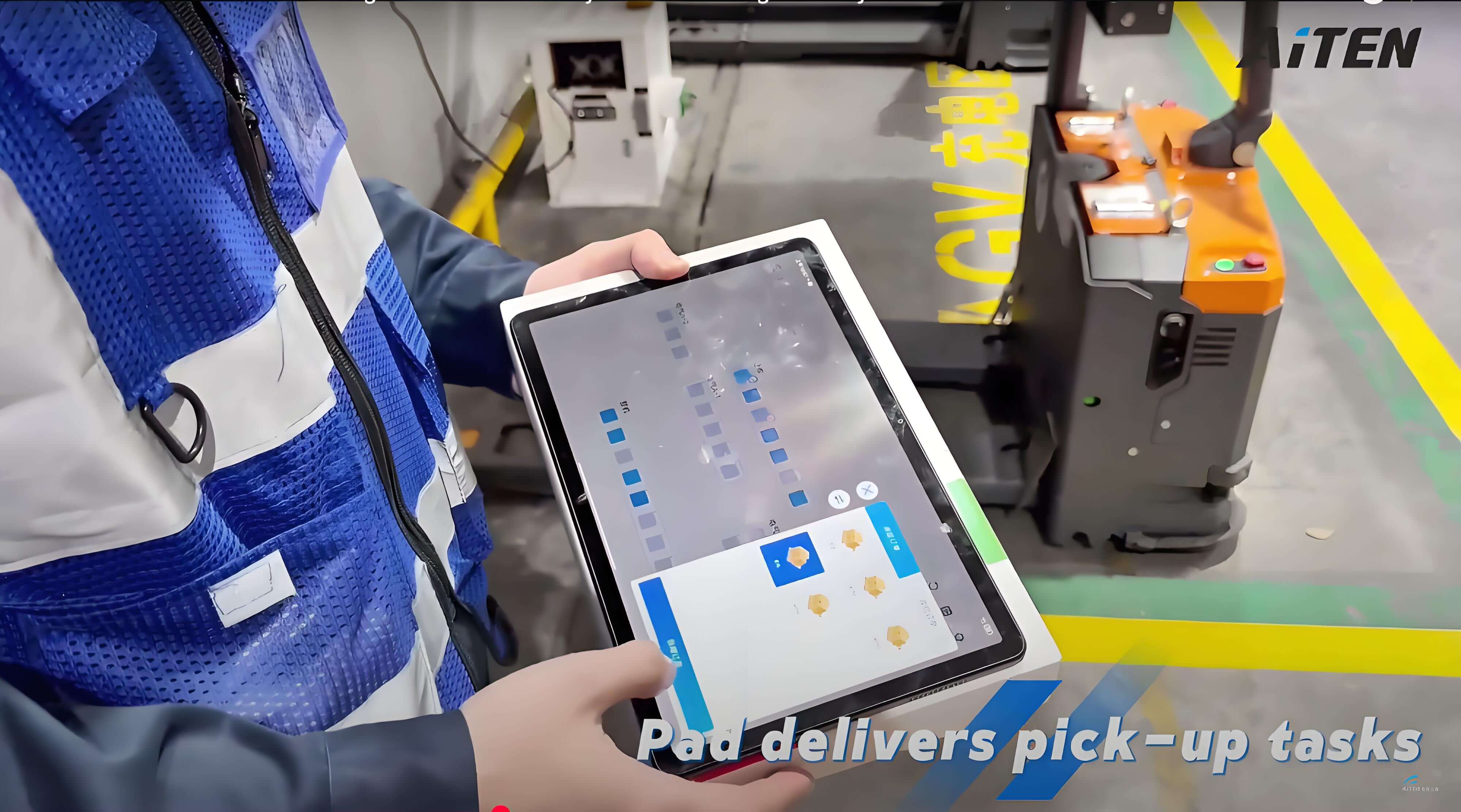
2. Intelligent Response
The APe15 robot autonomously plans the optimal path within 5 seconds, avoiding congested areas.
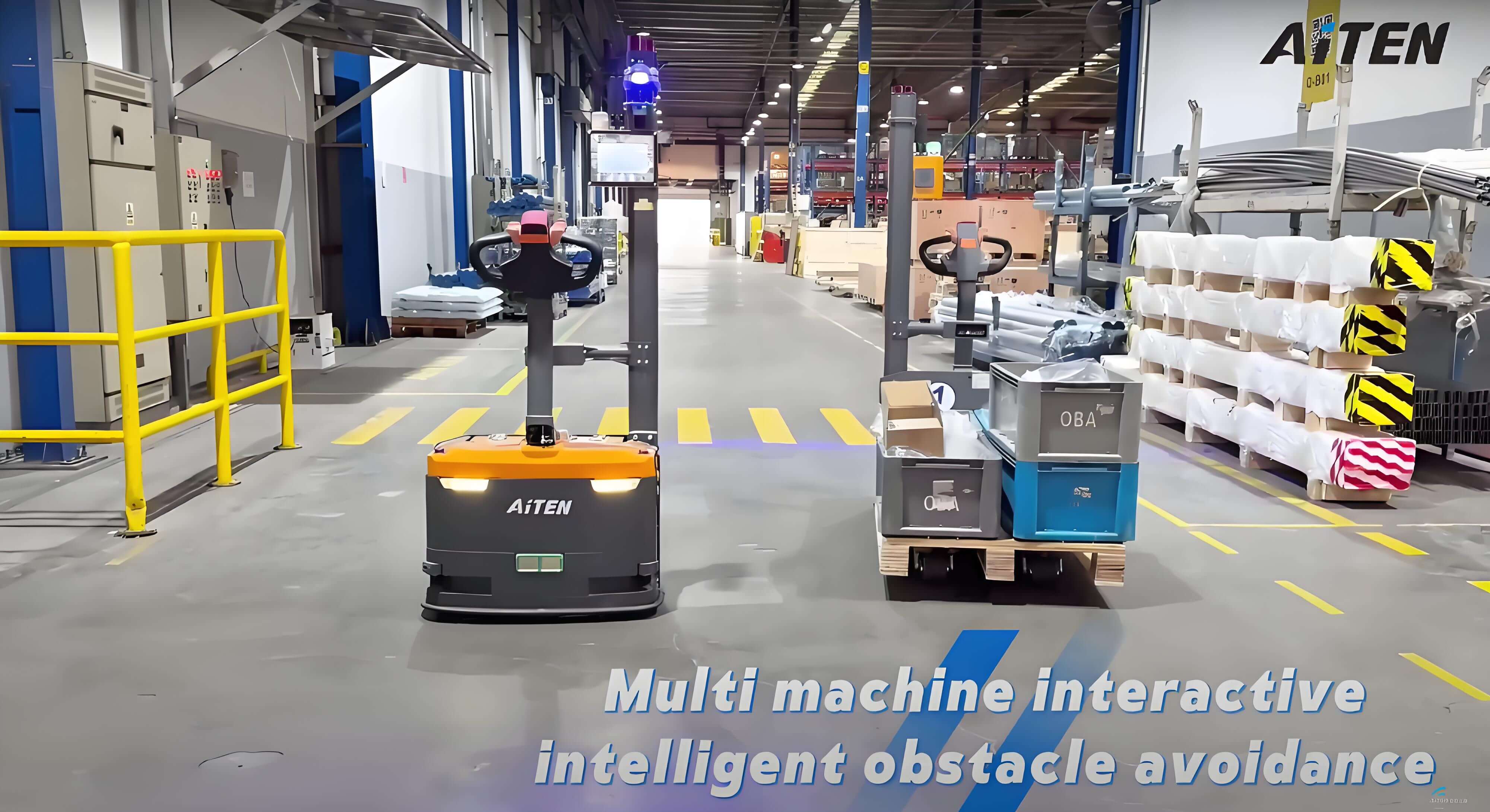
3. Safe passage
Multi-machine co-operation and automatic avoidance, accurate docking of automatic doors/elevators to achieve cross-area operation.
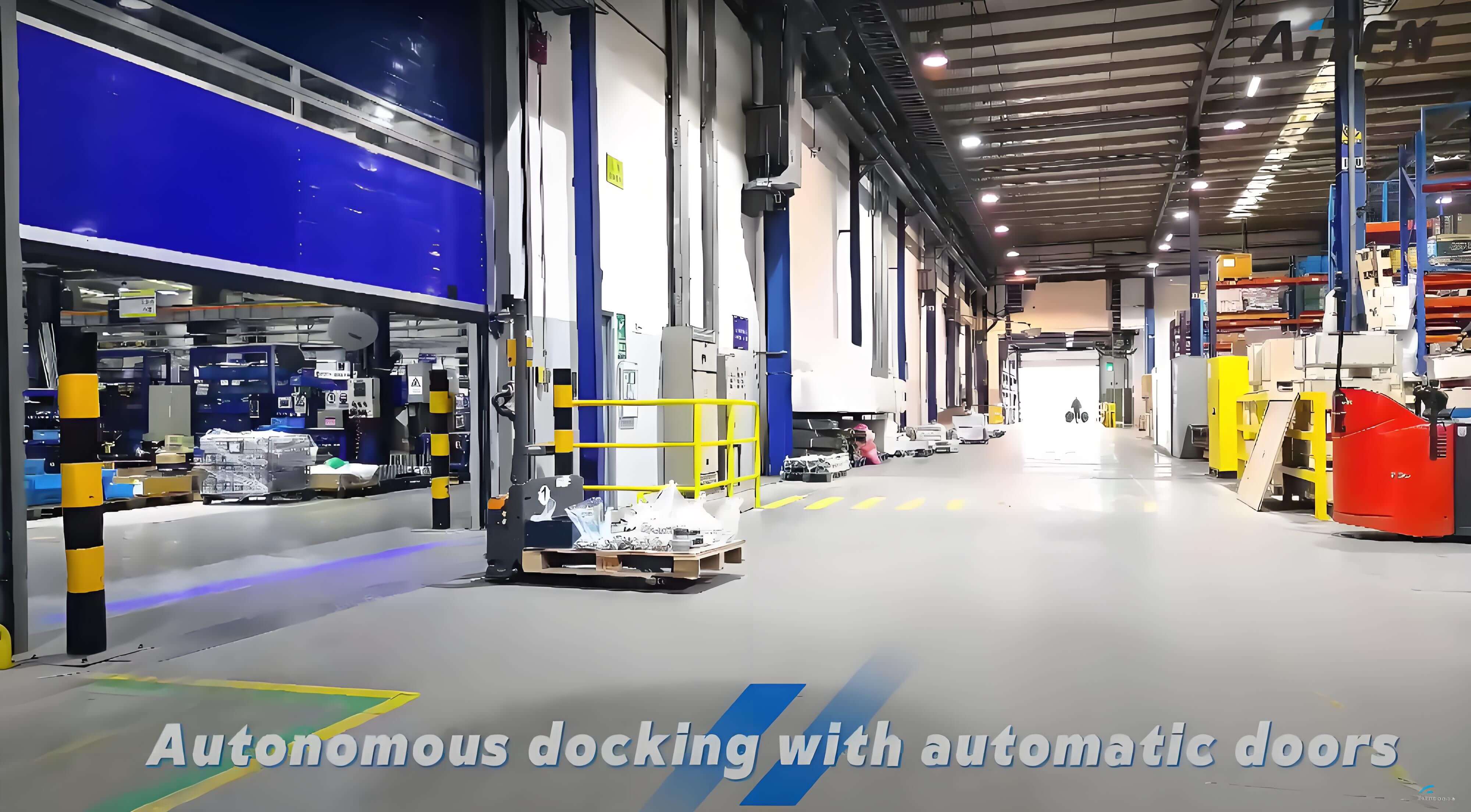
4. Precise Operation
Laser positioning ±5mm docking accuracy, complete lineside loading, and empty pallet recovery.
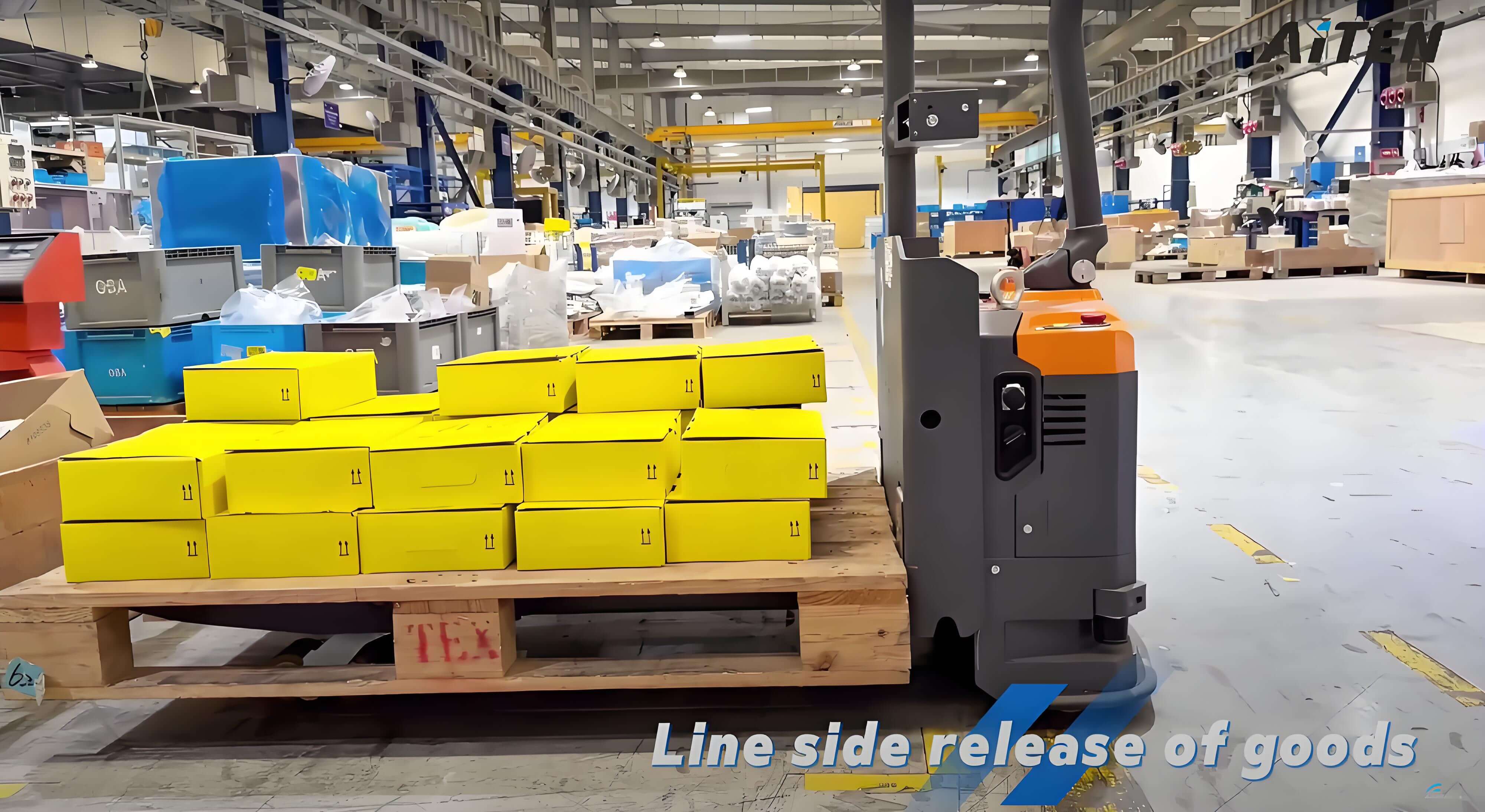
5. Closed-Loop Data
LMS system records the whole process node data, synchronised to the cloud to generate optimization suggestions.
Project Results
Through the combination of the APe15+RDS+LMS system, we create a whole-process intelligent logistics solution for the textile machinery manufacturing industry, which achieves:
√ Efficiency multiplication: 7*24h continuous operation, handling efficiency increased significantly.
√ Cost reconstruction: annual savings of 2 porters.
√ Management upgrade: real-time data-driven decision-making and faster response to exceptions.
For businesses facing similar challenges, AiTEN’s handling solution offers a proven path to operational excellence. Contact AiTEN today to learn how our innovative robotics and intelligent systems can transform your material handling processes.